大家好!今天让小编来大家介绍下关于无锡制氧机外壳模具设计_无锡制氧机外壳模具设计招聘的问题,以下是小编对此问题的归纳整理,让我们一起来看看吧。
文章目录列表:
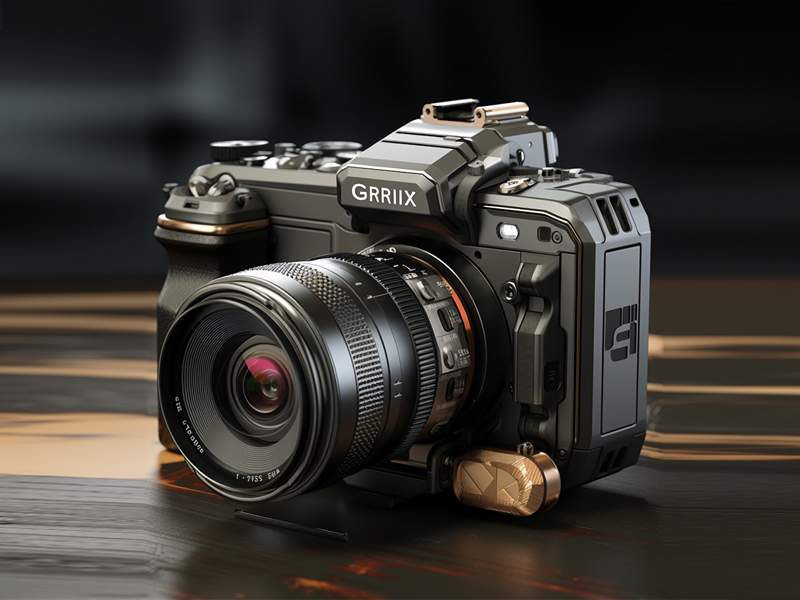
一、做模具流程图
模具制作流程
一、接受任务书
成型塑料制件的任务书通常由制件设计者提出,其内容如下:
1. 经过审签的正规制制件图纸,并注明采用塑料的牌号、透明度等。
2. 塑料制件说明书或技术要求。
3. 生产产量。
4. 塑料制件样品。
通常模具设计任务书由塑料制件工艺员根据成型塑料制件的任务书提出,模具设计人员以成型塑料制件任务书、模具设计任务书为依据来设计模具。
二、 收集、分析、消化原始资料
收集整理有关制件设计、成型工艺、成型设备、机械加工及特殊加工资料,以备设计模具时使用。
1. 消化塑料制件图,了解制件的用途,分析塑料制件的工艺性,尺寸精度等技术要求。例如塑料制件在外表形状、颜色透明度、使用性能方面的要求是什么,塑件的几何结构、斜度、嵌件等情况是否合理,熔接痕、缩孔等成型缺陷的允许程度,有无涂装、电镀、胶接、钻孔等后加工。选择塑料制件尺寸精度最高的尺寸进行分析,看看估计成型公差是否低于塑料制件的公差,能否成型出合乎要求的塑料制件来。此外,还要了解塑料的塑化及成型工艺参数。
2. 消化工艺资料,分析工艺任务书所提出的成型方法、设备型号、材料规格、模具结构类型等要求是否恰当,能否落实。
成型材料应当满足塑料制件的强度要求,具有好的流动性、均匀性和各向同性、热稳定性。根据塑料制件的用途,成型材料应满足染色、镀金属的条件、装饰性能、必要的弹性和塑性、透明性或者相反的反射性能、胶接性或者焊接性等要求。
3. 确定成型方法
采用直压法、铸压法还是注射法。
4、选择成型设备
根据成型设备的种类来进行模具,因此必须熟知各种成型设备的性能、规格、特点。例如对于注射机来说,在规格方面应当了解以下内容:注射容量、锁模压力、注射压力、模具安装尺寸、顶出装置及尺寸、喷嘴孔直径及喷嘴球面半径、浇口套定位圈尺寸、模具最大厚度和最小厚度、模板行程等,具体见相关参数。
要初步估计模具外形尺寸,判断模具能否在所选的注射机上安装和使用。
5. 具体结构方案
(一)确定模具类型
如压制模(敞开式、半闭合式、闭合式)、铸压模、注射模等。
(二)确定模具类型的主要结构
选择理想的模具结构在于确定必需的成型设备,理想的型腔数,在绝对可靠的条件下能使模具本身的工作满足该塑料制件的工艺技术和生产经济的要求。对塑料制件的工艺技术要求是要保证塑料制件的几何形状,表面光洁度和尺寸精度。生产经济要求是要使塑料制件的成本低,生产效率高,模具能连续地工作,使用寿命长,节省劳动力。
三、影响模具结构及模具个别系统的因素很多,很复杂:
1. 型腔布置。根据塑件的几何结构特点、尺寸精度要求、批量大小、模具制造难易、模具成本等确定型腔数量及其排列方式。
对于注射模来说,塑料制件精度为3级和3a级,重量为5克,采用硬化浇注系统,型腔数取4-6个;塑料制件为一般精度(4-5级),成型材料为局部结晶材料,型腔数可取16-20个;塑料制件重量为12-16克,型腔数取8-12个;而重量为50-100克的塑料制件,型腔数取4-8个。对于无定型的塑料制件建议型腔数为24-48个,16-32个和6-10个。当再继续增加塑料制件重量时,就很少采用多腔模具。7-9级精度的塑料制件,最多型腔数较之指出的4-5级精度的塑料增多至50%。
2. 确定分型面。分型面的位置要有利于模具加工,排气、脱模及成型操作,塑料制件的表面质量等。
3. 确定浇注系统(主浇道、分浇道及浇口的形状、位置、大小)和排气系统(排气的方法、排气槽位置、大小)。
4. 选择顶出方式(顶杆、顶管、推板、组合式顶出),决定侧凹处理方法、抽芯方式。
5. 决定冷却、加热方式及加热冷却沟槽的形状、位置、加热元件的安装部位。
6. 根据模具材料、强度计算或者经验数据,确定模具零件厚度及外形尺寸,外形结构及所有连接、定位、导向件位置。
7. 确定主要成型零件,结构件的结构形式。
8. 考虑模具各部分的强度,计算成型零件工作尺寸。
以上这些问题如果解决了,模具的结构形式自然就解决了。这时,就应该着手绘制模具结构草图,为正式绘图作好准备。
四、绘制模具图
要求按照国家制图标准绘制,但是也要求结合本厂标准和国家未规定的工厂习惯画法。
在画模具总装图之前,应绘制工序图,并要符合制件图和工艺资料的要求。由下道工序保证的尺寸,应在图上标写注明"工艺尺寸"字样。如果成型后除了修理毛刺之外,再不进行其他机械加工,那么工序图就与制件图完全相同。
在工序图下面最好标出制件编号、名称、材料、材料收缩率、绘图比例等。通常就把工序图画在模具总装图上。
1. 绘制总装结构图
绘制总装图尽量采用1:1的比例,先由型腔开始绘制,主视图与其它视图同时画出。
五、模具总装图应包括以下内容:
1. 模具成型部分结构
2. 浇注系统、排气系统的结构形式。
3. 分型面及分模取件方式。
4. 外形结构及所有连接件,定位、导向件的位置。
5. 标注型腔高度尺寸(不强求,根据需要)及模具总体尺寸。
6. 辅助工具(取件卸模工具,校正工具等)。
7. 按顺序将全部零件序号编出,并且填写明细表。
8. 标注技术要求和使用说明。
六、模具总装图的技术要求内容:
1. 对于模具某些系统的性能要求。例如对顶出系统、滑块抽芯结构的装配要求。
2. 对模具装配工艺的要求。例如模具装配后分型面的贴合面的贴合间隙应不大于0.05mm模具上、下面的平行度要求,并指出由装配决定的尺寸和对该尺寸的要求。
3. 模具使用,装拆方法。
4. 防氧化处理、模具编号、刻字、标记、油封、保管等要求。
5. 有关试模及检验方面的要求。
七、绘制全部零件图
由模具总装图拆画零件图的顺序应为:先内后外,先复杂后简单,先成型零件,后结构零件。
1. 图形要求:一定要按比例画,允许放大或缩小。视图选择合理,投影正确,布置得当。为了使加工专利号易看懂、便于装配,图形尽可能与总装图一致,图形要清晰。
2. 标注尺寸要求统一、集中、有序、完整。标注尺寸的顺序为:先标主要零件尺寸和出模斜度,再标注配合尺寸,然后标注全部尺寸。在非主要零件图上先标注配合尺寸,后标注全部尺寸。
3. 表面粗糙度。把应用最多的一种粗糙度标于图纸右上角,如标注"其余3.2。"其它粗糙度符号在零件各表面分别标出。
4. 其它内容,例如零件名称、模具图号、材料牌号、热处理和硬度要求,表面处理、图形比例、自由尺寸的加工精度、技术说明等都要正确填写。
八、.校对、审图、描图、送晒
A.自广东会对的内容是:
1. 模具及其零件与塑件图纸的关系
模具及模具零件的材质、硬度、尺寸精度,结构等是否符合塑件图纸的要求。
2. 塑料制件方面
塑料料流的流动、缩孔、熔接痕、裂口,脱模斜度等是否影响塑料制件的使用性能、尺寸精度、表面质量等方面的要求。图案设计有无不足,加工是否简单,成型材料的收缩率选用是否正确。
3. 成型设备方面
注射量、注射压力、锁模力够不够,模具的安装、塑料制件的南芯、脱模有无问题,注射机的喷嘴与哓口套是否正确地接触。
4. 模具结构方面
1). 分型面位置及精加工精度是否满足需要,会不会发生溢料,开模后是否能保证塑料制件留在有顶出装置的模具一边。
2). 脱模方式是否正确,推广杆、推管的大小、位置、数量是否合适,推板会不会被型芯卡住,会不会造成擦伤成型零件。
3). 模具温度调节方面。加热器的功率、数量;冷却介质的流动线路位置、大小、数量是否合适。
4). 处理塑料制件制侧凹的方法,脱侧凹的机构是否恰当,例如斜导柱抽芯机构中的滑块与推杆是否相互干扰。
5). 浇注、排气系统的位置,大小是否恰当。
5. 设计图纸
1). 装配图上各模具零件安置部位是否恰当,表示得是否清楚,有无遗漏
2). 零件图上的零件编号、名称,制作数量、零件内制还是外购的,是标准件还是非标准件,零件配合处理精度、成型塑料制件高精度尺寸处的修正加工及余量,模具零件的材料、热处理、表面处理、表面精加工程度是否标记、叙述清楚。
3). 零件主要零件、成型零件工作尺寸及配合尺寸。尺寸数字应正确无误,不要使生产者换算。
4). 检查全部零件图及总装图的视图位置,投影是否正确,画法是否符合制图国标,有无遗漏尺寸。
6. 校核加工性能
(所有零件的几何结构、视图画法、尺寸标'等是否有利于加工)
7. 复算辅助工具的主要工作尺寸
B.专业校对原则上按设计者自广东会对项目进行;但是要侧重于结构原理、工艺性能及操作安全方面。
描图时要先消化图形,按国标要求描绘,填写全部尺寸及技术要求。描后自校并且签字。
C.把描好的底图交设计者校对签字,习惯做法是由工具制造单位有关技术人员审查,会签、检查制造工艺性,然后才可送晒。
D..编写制造工艺卡片
由工具制造单位技术人员编写制造工艺卡片,并且为加工制造做好准备。
在模具零件的制造过程中要加强检验,把检验的重点放在尺寸精度上。模具组装完成后,由检验员根据模具检验表进行检验,主要的是检验模具零件的性能情况是否良好,只有这样才能俚语模具的制造质量。
九、试模及修模
虽然是在选定成型材料、成型设备时,在预想的工艺条件下进行模具设计,但是人们的认识往往是不完善的,因此必须在模具加工完成以后,进行试模试验,看成型的制件质量如何。发现总是以后,进行排除错误性的修模。
塑件出现不良现象的种类居多,原因也很复杂,有模具方面的原因,也有工艺条件方面的原因,二者往往交只在一起。在修模前,应当根据塑件出现的不良现象的实际情况,进行细致地分析研究,找出造成塑件缺陷的原因后提出补救方法。因为成型条件容易改变,所以一般的做法是先变更成型条件,当变更成型条件不能解决问题时,才考虑修理模具。
修理模具更应慎重,没有十分把握不可轻举妄动。其原因是一旦变更了模具条件,就不能再作大的改造和恢复原状。
十、整理资料进行归档
模具经试验后,若暂不使用,则应该完全擦除脱模渣滓、灰尘、油污等,涂上黄油或其他防锈油或防锈剂,关到保管场所保管。
把设计模具开始到模具加工成功,检验合格为止,在此期间所产生的技术资料,例如任务书、制件图、技术说明书、模具总装图、模具零件图、底图、模具设计说明书、检验记录表、试模修模记录等,按规定加以系统整理、装订、编号进行归档。这样做似乎很麻烦,但是对以后修理模具,设计新的模具都是很有用处的。
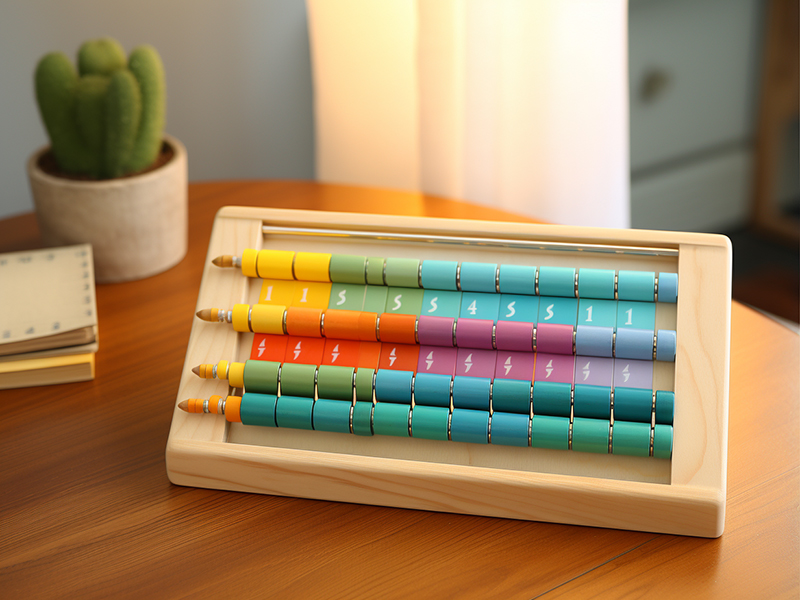
二、模具的设计重点在那些方面
模具设计步骤一、接受任务书 成型塑料制件的任务书通常由制件设计者提出,其内容如下: ⑴经过审签的正规制制件图纸,并注明采用塑料的牌号、透明度等。 ⑵塑料制件说明书或技术要求。 ⑶生产产量。 ⑷塑料制件样品。 通常模具设计任务书由塑料制件工艺员根据成型塑料制件的任务书提出,模具设计人员以成型塑料制件任务书、模具设计任务书为依据来设计模具。二、收集、分析、消化原始资料 收集整理有关制件设计、成型工艺、成型设备、机械加工及特殊加工资料,以备设计模具时使用。 ⑴消化塑料制件图,了解制件的用途,分析塑料制件的工艺性,尺寸精度等技术要求。例如塑料制件在外表形状、颜色透明度、使用性能方面的要求是什么,塑件的几何结构、斜度、嵌件等情况是否合理,熔接痕、缩孔等成型缺陷的允许程度,有无涂装、电镀、胶接、钻孔等后加工。选择塑料制件尺寸精度最高的尺寸进行分析,看看估计成型公差是否低于塑料制件的公差,能否成型出合乎要求的塑料制件来。此外,还要了解塑料的塑化及成型工艺参数。 ⑵消化工艺资料,分析工艺任务书所提出的成型方法、设备型号、材料规格、模具结构类型等要求是否恰当,能否落实。 成型材料应当满足塑料制件的强度要求,具有好的流动性、均匀性和各向同性、热稳定性。根据塑料制件的用途,成型材料应满足染色、镀金属的条件、装饰性能、必要的弹性和塑性、透明性或者相反的反射性能、胶接性或者焊接性等要求。三、确定成型方法 采用直压法、铸压法还是注射法。四、选择成型设备 根据成型设备的种类来进行模具,因此必须熟知各种成型设备的性能、规格、特点。例如对于注射机来说,在规格方面应当了解以下内容:注射容量、锁模压力、注射压力、模具安装尺寸、顶出装置及尺寸、喷嘴孔直径及喷嘴球面半径、浇口套定位圈尺寸、模具最大厚度和最小厚度、模板行程等,具体见相关参数。 要初步估计模具外形尺寸,判断模具能否在所选的注射机上安装和使用。 五、具体结构方案: ⑴确定模具类型 如压制模(敞开式、半闭合式、闭合式)、铸压模、注射模等。 ⑵确定模具类型的主要结构 选择理想的模具结构在于确定必需的成型设备,理想的型腔数,在绝对可靠的条件下能使模具本身的工作满足该塑料制件的工艺技术和生产经济的要求。对塑料制件的工艺技术要求是要保证塑料制件的几何形状,表面光洁度和尺寸精度。生产经济要求是要使塑料制件的成本低,生产效率高,模具能连续地工作,使用寿命长,节省劳动力。 影响模具结构及模具个别系统的因素很多,很复杂: ①型腔布置。根据塑件的几何结构特点、尺寸精度要求、批量大小、模具制造难易、模具成本等确定型腔数量及其排列方式。 对于注射模来说,塑料制件精度为3级和3a级,重量为5克,采用硬化浇注系统,型腔数取4-6个;塑料制件为一般精度(4-5级),成型材料为局部结晶材料,型腔数可取 16-20个;塑料制件重量为12-16克,型腔数取8-12个;而重量为50-100克的塑料制件,型腔数取4-8个。对于无定型的塑料制件建议型腔数为24-48个,16-32个和6-10个。当再继续增加塑料制件重量时,就很少采用多腔模具。7-9级精度的塑料制件,最多型腔数较之指出的4-5 级精度的塑料增多至50%。 ②确定分型面。分型面的位置要有利于模具加工,排气、脱模及成型操作,塑料制件的表面质量等。 ③确定浇注系统(主浇道、分浇道及浇口的形状、位置、大小)和排气系统(排气的方法、排气槽位置、大小)。 ④选择顶出方式(顶杆、顶管、推板、组合式顶出),决定侧凹处理方法、抽芯方式。 ⑤决定冷却、加热方式及加热冷却沟槽的形状、位置、加热元件的安装部位。 ⑥根据模具材料、强度计算或者经验数据,确定模具零件厚度及外形尺寸,外形结构及所有连接、定位、导向件位置。 ⑦确定主要成型零件,结构件的结构形式。 ⑧考虑模具各部分的强度,计算成型零件工作尺寸。 以上这些问题如果解决了,模具的结构形式自然就解决了。这时,就应该着手绘制模具结构草图,为正式绘图作好准备。 ⑨绘制模具图 要求按照国家制图标准绘制,但是也要求结合本厂标准和国家未规定的工厂习惯画法。 在画模具总装图之前,应绘制工序图,并要符合制件图和工艺资料的要求。由下道工序保证的尺寸,应在图上标写注明"工艺尺寸"字样。如果成型后除了修理毛刺之外,再不进行其他机械加工,那么工序图就与制件图完全相同。 在工序图下面最好标出制件编号、名称、材料、材料收缩率、绘图比例等。通常就把工序图画在模具总装图上。 A、绘制总装结构图 绘制总装图尽量采用1:1的比例,先由型腔开始绘制,主视图与其它视图同时画出。 模具总装图应包括以下内容: ①模具成型部分结构 ②浇注系统、排气系统的结构形式。 ③分型面及分模取件方式。 ④外形结构及所有连接件,定位、导向件的位置。 ⑤标注型腔高度尺寸(不强求,根据需要)及模具总体尺寸。 ⑥辅助工具(取件卸模工具,校正工具等)。 ⑦按顺序将全部零件序号编出,并且填写明细表。 ⑧标注技术要求和使用说明。 B、模具总装图的技术要求内容: ①对于模具某些系统的性能要求。例如对顶出系统、滑块抽芯结构的装配要求。 ②对模具装配工艺的要求。例如模具装配后分型面的贴合面的贴合间隙应不大于0.05mm模具上、下面的平行度要求,并指出由装配决定的尺寸和对该尺寸的要求。 ③模具使用,装拆方法。 ④防氧化处理、模具编号、刻字、标记、油封、保管等要求。 ⑤有关试模及检验方面的要求。 C、绘制全部零件图 由模具总装图拆画零件图的顺序应为:先内后外,先复杂后简单,先成型零件,后结构零件。 ①图形要求:一定要按比例画,允许放大或缩小。视图选择合理,投影正确,布置得当。为了使加工专利号易看懂、便于装配,图形尽可能与总装图一致,图形要清晰。 ②标注尺寸要求统一、集中、有序、完整。标注尺寸的顺序为:先标主要零件尺寸和出模斜度,再标注配合尺寸,然后标注全部尺寸。在非主要零件图上先标注配合尺寸,后标注全部尺寸。 ③表面粗糙度。把应用最多的一种粗糙度标于图纸右上角,如标注"其余3.2。 "其它粗糙度符号在零件各表面分别标出。 ④其它内容,例如零件名称、模具图号、材料牌号、热处理和硬度要求,表面处理、图形比例、自由尺寸的加工精度、技术说明等都要正确填写。 D、校对、审图、描图、送晒 自广东会对的内容是: ①模具及其零件与塑件图纸的关系,模具及模具零件的材质、硬度、尺寸精度,结构等是否符合塑件图纸的要求。 ②塑料制件方面 塑料料流的流动、缩孔、熔接痕、裂口,脱模斜度等是否影响塑料制件的使用性能、尺寸精度、表面质量等方面的要求。图案设计有无不足,加工是否简单,成型材料的收缩率选用是否正确。 ③成型设备方面 注射量、注射压力、锁模力够不够,模具的安装、塑料制件的南芯、脱模有无问题,注射机的喷嘴与哓口套是否正确地接触。 ④模具结构方面 a.分型面位置及精加工精度是否满足需要,会不会发生溢料,开模后是否能保证塑料制件留在有顶出装置的模具一边。 b.脱模方式是否正确,推广杆、推管的大小、位置、数量是否合适,推板会不会被型芯卡住,会不会造成擦伤成型零件。 c.模具温度调节方面。加热器的功率、数量;冷却介质的流动线路位置、大小、数量是否合适。 d.处理塑料制件制侧凹的方法,脱侧凹的机构是否恰当,例如斜导柱抽芯机构中的滑块与推杆是否相互干扰。 e.浇注、排气系统的位置,大小是否恰当。 f.设计图纸 g.装配图上各模具零件安置部位是否恰当,表示得是否清楚,有无遗漏 h.零件图上的零件编号、名称,制作数量、零件内制还是外购的,是标准件还是非标准件,零件配合处理精度、成型塑料制件高精度尺寸处的修正加工及余量,模具零件的材料、热处理、表面处理、表面精加工程度是否标记、叙述清楚。⑤零件主要零件、成型零件工作尺寸及配合尺寸。尺寸数字应正确无误,不要使生产者换算。⑥检查全部零件图及总装图的视图位置,投影是否正确,画法是否符合制图国标,有无遗漏尺寸。⑦校核加工性能:(所有零件的几何结构、视图画法、尺寸标'等是否有利于加工)⑧复算辅助工具的主要工作尺寸专业校对原则上按设计者自广东会对项目进行;但是要侧重于结构原理、工艺性能及操作安全方面。描图时要先消化图形,按国标要求描绘,填写全部尺寸及技术要求。描后自校并且签字。把描好的底图交设计者校对签字,习惯做法是由工具制造单位有关技术人员审查,会签、检查制造工艺性,然后才可送晒。⑨编写制造工艺卡片由工具制造单位技术人员编写制造工艺卡片,并且为加工制造做好准备。在模具零件的制造过程中要加强检验,把检验的重点放在尺寸精度上。模具组装完成后,由检验员根据模具检验表进行检验,主要的是检验模具零件的性能情况是否良好,只有这样才能俚语模具的制造质量。 ⑶试模及修模 虽然是在选定成型材料、成型设备时,在预想的工艺条件下进行模具设计,但是人们的认识往往是不完善的,因此必须在模具加工完成以后,进行试模试验,看成型的制件质量如何。发现总是以后,进行排除错误性的修模。 塑件出现不良现象的种类居多,原因也很复杂,有模具方面的原因,也有工艺条件方面的原因,二者往往交只在一起。在修模前,应当根据塑件出现的不良现象的实际情况,进行细致地分析研究,找出造成塑件缺陷的原因后提出补救方法。因为成型条件容易改变,所以一般的做法是先变更成型条件,当变更成型条件不能解决问题时,才考虑修理模具。 修理模具更应慎重,没有十分把握不可轻举妄动。其原因是一旦变更了模具条件,就不能再作大的改造和恢复原状。六、整理资料进行归档 模具经试验后,若暂不使用,则应该完全擦除脱模渣滓、灰尘、油污等,涂上黄油或其他防锈油或防锈剂,关到保管场所保管。 把设计模具开始到模具加工成功,检验合格为止,在此期间所产生的技术资料,例如任务书、制件图、技术说明书、模具总装图、模具零件图、底图、模具设计说明书、检验记录表、试模修模记录等,按规定加以系统整理、装订、编号进行归档。这样做似乎很麻烦,但是对以后修理模具,设计新的模具都是很有用处的
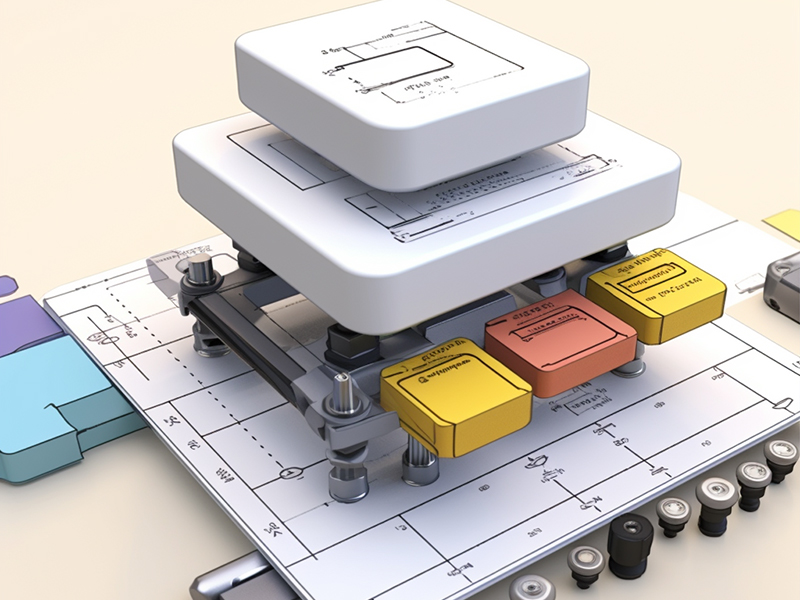
三、塑胶模具行位做法与技巧
模具设计步骤
一、接受任务书
成型塑料制件的任务书通常由制件设计者提出,其内容如下: ⑴经过审签的正规制制件图纸,并注明采用塑料的牌号、透明度等。 ⑵塑料制件说明书或技术要求。 ⑶生产产量。 ⑷塑料制件样品。 通常模具设计任务书由塑料制件工艺员根据成型塑料制件的任务书提出,模具设计人员以成型塑料制件任务书、模具设计任务书为依据来设计模具。
二、收集、分析、消化原始资料
收集整理有关制件设计、成型工艺、成型设备、机械加工及特殊加工资料,以备设计模具时使用。 ⑴消化塑料制件图,了解制件的用途,分析塑料制件的工艺性,尺寸精度等技术要求。例如塑料制件在外表形状、颜色透明度、使用性能方面的要求是什么,塑件的几何结构、斜度、嵌件等情况是否合理,熔接痕、缩孔等成型缺陷的允许程度,有无涂装、电镀、胶接、钻孔等后加工。选择塑料制件尺寸精度最高的尺寸进行分析,看看估计成型公差是否低于塑料制件的公差,能否成型出合乎要求的塑料制件来。此外,还要了解塑料的塑化及成型工艺参数。 ⑵消化工艺资料,分析工艺任务书所提出的成型方法、设备型号、材料规格、模具结构类型等要求是否恰当,能否落实。 成型材料应当满足塑料制件的强度要求,具有好的流动性、均匀性和各向同性、热稳定性。根据塑料制件的用途,成型材料应满足染色、镀金属的条件、装饰性能、必要的弹性和塑性、透明性或者相反的反射性能、胶接性或者焊接性等要求。
三、确定成型方法
采用直压法、铸压法还是注射法。
四、选择成型设备
根据成型设备的种类来进行模具,因此必须熟知各种成型设备的性能、规格、特点。例如对于注射机来说,在规格方面应当了解以下内容:注射容量、锁模压力、注射压力、模具安装尺寸、顶出装置及尺寸、喷嘴孔直径及喷嘴球面半径、浇口套定位圈尺寸、模具最大厚度和最小厚度、模板行程等,具体见相关参数。 要初步估计模具外形尺寸,判断模具能否在所选的注射机上安装和使用。
五、具体结构方案:
⑴确定模具类型 如压制模(敞开式、半闭合式、闭合式)、铸压模、注射模等。
⑵确定模具类型的主要结构 选择理想的模具结构在于确定必需的成型设备,理想的型腔数,在绝对可靠的条件下能使模具本身的工作满足该塑料制件的工艺技术和生产经济的要求。对塑料制件的工艺技术要求是要保证塑料制件的几何形状,表面光洁度和尺寸精度。生产经济要求是要使塑料制件的成本低,生产效率高,模具能连续地工作,使用寿命长,节省劳动力。
影响模具结构及模具个别系统的因素很多,很复杂:
①型腔布置。根据塑件的几何结构特点、尺寸精度要求、批量大小、模具制造难易、模具成本等确定型腔数量及其排列方式。 对于注射模来说,塑料制件精度为3级和3a级,重量为5克,采用硬化浇注系统,型腔数取4-6个;塑料制件为一般精度(4-5级),成型材料为局部结晶材料,型腔数可取 16-20个;塑料制件重量为12-16克,型腔数取8-12个;而重量为50-100克的塑料制件,型腔数取4-8个。对于无定型的塑料制件建议型腔数为24-48个,16-32个和6-10个。当再继续增加塑料制件重量时,就很少采用多腔模具。7-9级精度的塑料制件,最多型腔数较之指出的4-5 级精度的塑料增多至50%。 ②确定分型面。分型面的位置要有利于模具加工,排气、脱模及成型操作,塑料制件的表面质量等。
③确定浇注系统(主浇道、分浇道及浇口的形状、位置、大小)和排气系统(排气的方法、排气槽位置、大小)。
④选择顶出方式(顶杆、顶管、推板、组合式顶出),决定侧凹处理方法、抽芯方式。
⑤决定冷却、加热方式及加热冷却沟槽的形状、位置、加热元件的安装部位。
⑥根据模具材料、强度计算或者经验数据,确定模具零件厚度及外形尺寸,外形结构及所有连接、定位、导向件位置。
⑦确定主要成型零件,结构件的结构形式。
⑧考虑模具各部分的强度,计算成型零件工作尺寸。 以上这些问题如果解决了,模具的结构形式自然就解决了。这时,就应该着手绘制模具结构草图,为正式绘图作好准备。
⑨绘制模具图 要求按照国家制图标准绘制,但是也要求结合本厂标准和国家未规定的工厂习惯画法。 在画模具总装图之前,应绘制工序图,并要符合制件图和工艺资料的要求。由下道工序保证的尺寸,应在图上标写注明"工艺尺寸"字样。如果成型后除了修理毛刺之外,再不进行其他机械加工,那么工序图就与制件图完全相同。 在工序图下面最好标出制件编号、名称、材料、材料收缩率、绘图比例等。通常就把工序图画在模具总装图上。 A、绘制总装结构图 绘制总装图尽量采用1:1的比例,先由型腔开始绘制,主视图与其它视图同时画出。 模具总装图应包括以下内容: ①模具成型部分结构 ②浇注系统、排气系统的结构形式。 ③分型面及分模取件方式。 ④外形结构及所有连接件,定位、导向件的位置。 ⑤标注型腔高度尺寸(不强求,根据需要)及模具总体尺寸。 ⑥辅助工具(取件卸模工具,校正工具等)。 ⑦按顺序将全部零件序号编出,并且填写明细表。 ⑧标注技术要求和使用说明。 B、模具总装图的技术要求内容: ①对于模具某些系统的性能要求。例如对顶出系统、滑块抽芯结构的装配要求。 ②对模具装配工艺的要求。例如模具装配后分型面的贴合面的贴合间隙应不大于0.05mm模具上、下面的平行度要求,并指出由装配决定的尺寸和对该尺寸的要求。 ③模具使用,装拆方法。 ④防氧化处理、模具编号、刻字、标记、油封、保管等要求。 ⑤有关试模及检验方面的要求。 C、绘制全部零件图 由模具总装图拆画零件图的顺序应为:先内后外,先复杂后简单,先成型零件,后结构零件。 ①图形要求:一定要按比例画,允许放大或缩小。视图选择合理,投影正确,布置得当。为了使加工专利号易看懂、便于装配,图形尽可能与总装图一致,图形要清晰。 ②标注尺寸要求统一、集中、有序、完整。标注尺寸的顺序为:先标主要零件尺寸和出模斜度,再标注配合尺寸,然后标注全部尺寸。在非主要零件图上先标注配合尺寸,后标注全部尺寸。 ③表面粗糙度。把应用最多的一种粗糙度标于图纸右上角,如标注"其余3.2。 "其它粗糙度符号在零件各表面分别标出。 ④其它内容,例如零件名称、模具图号、材料牌号、热处理和硬度要求,表面处理、图形比例、自由尺寸的加工精度、技术说明等都要正确填写。 D、校对、审图、描图、送晒 自广东会对的内容是: ①模具及其零件与塑件图纸的关系,模具及模具零件的材质、硬度、尺寸精度,结构等是否符合塑件图纸的要求。 ②塑料制件方面 塑料料流的流动、缩孔、熔接痕、裂口,脱模斜度等是否影响塑料制件的使用性能、尺寸精度、表面质量等方面的要求。图案设计有无不足,加工是否简单,成型材料的收缩率选用是否正确。 ③成型设备方面 注射量、注射压力、锁模力够不够,模具的安装、塑料制件的南芯、脱模有无问题,注射机的喷嘴与哓口套是否正确地接触。 ④模具结构方面 a.分型面位置及精加工精度是否满足需要,会不会发生溢料,开模后是否能保证塑料制件留在有顶出装置的模具一边。 b.脱模方式是否正确,推广杆、推管的大小、位置、数量是否合适,推板会不会被型芯卡住,会不会造成擦伤成型零件。 c.模具温度调节方面。加热器的功率、数量;冷却介质的流动线路位置、大小、数量是否合适。 d.处理塑料制件制侧凹的方法,脱侧凹的机构是否恰当,例如斜导柱抽芯机构中的滑块与推杆是否相互干扰。 e.浇注、排气系统的位置,大小是否恰当。 f.设计图纸 g.装配图上各模具零件安置部位是否恰当,表示得是否清楚,有无遗漏 h.零件图上的零件编号、名称,制作数量、零件内制还是外购的,是标准件还是非标准件,零件配合处理精度、成型塑料制件高精度尺寸处的修正加工及余量,模具零件的材料、热处理、表面处理、表面精加工程度是否标记、叙述清楚。⑤零件主要零件、成型零件工作尺寸及配合尺寸。尺寸数字应正确无误,不要使生产者换算。⑥检查全部零件图及总装图的视图位置,投影是否正确,画法是否符合制图国标,有无遗漏尺寸。⑦校核加工性能:(所有零件的几何结构、视图画法、尺寸标'等是否有利于加工)⑧复算辅助工具的主要工作尺寸专业校对原则上按设计者自广东会对项目进行;但是要侧重于结构原理、工艺性能及操作安全方面。描图时要先消化图形,按国标要求描绘,填写全部尺寸及技术要求。描后自校并且签字。把描好的底图交设计者校对签字,习惯做法是由工具制造单位有关技术人员审查,会签、检查制造工艺性,然后才可送晒。⑨编写制造工艺卡片由工具制造单位技术人员编写制造工艺卡片,并且为加工制造做好准备。在模具零件的制造过程中要加强检验,把检验的重点放在尺寸精度上。模具组装完成后,由检验员根据模具检验表进行检验,主要的是检验模具零件的性能情况是否良好,只有这样才能俚语模具的制造质量。 ⑶试模及修模 虽然是在选定成型材料、成型设备时,在预想的工艺条件下进行模具设计,但是人们的认识往往是不完善的,因此必须在模具加工完成以后,进行试模试验,看成型的制件质量如何。发现总是以后,进行排除错误性的修模。 塑件出现不良现象的种类居多,原因也很复杂,有模具方面的原因,也有工艺条件方面的原因,二者往往交只在一起。在修模前,应当根据塑件出现的不良现象的实际情况,进行细致地分析研究,找出造成塑件缺陷的原因后提出补救方法。因为成型条件容易改变,所以一般的做法是先变更成型条件,当变更成型条件不能解决问题时,才考虑修理模具。 修理模具更应慎重,没有十分把握不可轻举妄动。其原因是一旦变更了模具条件,就不能再作大的改造和恢复原状。
六、整理资料进行归档 模具经试验后,若暂不使用,则应该完全擦除脱模渣滓、灰尘、油污等,涂上黄油或其他防锈油或防锈剂,关到保管场所保管。 把设计模具开始到模具加工成功,检验合格为止,在此期间所产生的技术资料,例如任务书、制件图、技术说明书、模具总装图、模具零件图、底图、模具设计说明书、检验记录表、试模修模记录等,按规定加以系统整理、装订、编号进行归档。这样做似乎很麻烦,但是对以后修理模具,设计新的模具都是很有用处的
四、有没有关于执行机构基础的书
执行机构讲义
一、执行机构的由来
执行机构,又称执行器,是一种自动控制领域的常用机电一体化设备(器件),是自动化仪表的三大组成部分(检测设备、调节设备和执行设备)中的执行设备。主要是对一些设备和装置进行自动操作,控制其开关和调节,代替人工作业。按动力类型可分为气动、液动、电动、电液动等几类;按运动形式可分为直行程、角行程、回转型(多转式)等几类。由于用电做为动力有其它几类介质不可比拟的优势,所以电动型近年来发展最快,应用面较广。电动型按不同标准又可分为:组合式结构和机电一体化结构;电器控制型、电子控制型和智能控制型(带HART、FF协议);数字型和模拟型;手动接触调试型和红外线遥控调试型等。它是伴随着人们对控制性能的要求和自动控制技术的发展而迅猛发展的:
1. 早期的工业领域,有许多的控制是手动和半自动的,在操作中人体直接接触工业设备的危险部位和危险介质(固、液、气三态的多种化学物质和辐射物质),极易造成对人的伤害,很不安全;
2. 设备寿命短、易损坏、维修量大;
3. 采用半自动特别是手动控制的控制效率很低、误差大,生产效率低下。
基于以上原因,执行机构逐渐产生并应用于工业和其它控制领域,减少和避免了人身伤害和设备损坏,极大的提高了控制精确度和效率,同时也极大提高了生产效率。今年来随着电子元器件技术、计算机技术和控制理论的飞速发展,国内外的执行机构都已跨入智能控制的时代。
二、执行机构的英文名:ACTUATORS
三、执行机构的应用领域
执行机构主要应用在以下三大领域:
1. 发电厂
典型应用有:
①火电行业应用
送风机风门挡板 一次进风风门挡板 空气预热风门挡板 烟气再循环 旁路风门挡板 二次进风风门挡板 主风箱风门挡板 燃烧器调节杆 燃烧器摇摆驱动器 液压推杆驱动器 叶轮机调速 烟气调节阀 蒸气调节阀 球阀和蝶阀控制 滑动门 闸门
②其它电力行业的阀门执行器应用
球阀 除尘控制喷水 叶轮机转速控制 控制大型液压阀 燃气控制阀 燃烧器点火启动 蒸气控制阀 冷凝水再循环, 脱氧机,锅炉给水,过热控制 器,再加热恒温控制器,及其它相关阀门应用
2. 过程控制
用于化工、石化、模具、食品、医药、包装等行业的生产过程控制,按照既定的逻辑指令或电脑程序对阀门、刀具、管道、挡板、滑槽、平台等进行精确的定位、起停、开合、回转,利用系统检测出的温度、压力、流量、尺寸、辐射、亮度、色度、粗糙度、密度等实时参数对系统进行调整,从而实现间歇、连续和循环的加工过程的控制。
3. 工业自动化
用于较为广泛的航空、航天、军工、机械、冶金、开采、交通、建材等方面,对各类自动化设备和系统的运动点(运动部件)进行各种形式的调节和控制。
过程控制和工业自动化方面的主要应用举例如下:
① 在硫矿生产中的应用
注水流量控制 球阀和碟阀控制
②碳酸钾管道阀门执行器的应用
滑动门 分流器 闸门 球阀和蝶阀 球型控制阀
③水处理阀门执行器的应用
液流流量控制 广东会阀压力控制 酸溶液流量控制
④石灰石/水泥厂阀门执行器的应用
球或蝶阀控制 处理干水泥,石膏,或液体 送风和引风机 调节型风门挡板 旁路风门挡板 环境污染控制和除尘装置 滑动门 对在料斗和储藏库的原材料进行物流控制 闸门 控制原材料在进料口的流量 燃气控制阀 调节转炉上燃烧器进气量 蒸气控制阀 控制生产过程所需的蒸气
⑤在谷物加工厂执行器的应用
闸门 分流阀 分配器 物料卸货器/加热器 除尘隔离挡板 气流控制(物流干燥) 球阀和蝶阀控制
⑥钢厂风门挡板和阀门执行器的应用
球或蝶阀控制 控制冷却水,废水,或其它冷却介质 调节型风门挡板 送风和引风机 旁路风门挡板 闸门 环境污染控制和除尘装置 滑动门 控制原材料在进料口的流量 对在料斗和储藏库的原材料进行物流控制 燃气控制阀 蒸气控制阀 调节转炉上燃烧器进气量 控制生产过程所需的蒸气
⑦铝厂风门挡板和阀门执行器的应用
送风机风门挡板 一次进风风门挡板 空气预热风门挡板 烟气再循环 旁路风门挡板 二次进风风门挡板 主风箱风门挡板 燃烧器调节杆 燃烧器摇摆驱动器 液压推杆驱动器 叶轮机调速 烟气调节阀 蒸气调节阀 球阀和蝶阀控制 滑动门 闸门
⑧过程控制挡板的应用
空气补充 排风机旁路 热/冷风混和 应急关断
⑨在石油工业中的应用
注油工艺流量控制 气举管路主阀门压力控制 注水工艺流量控制 油井油质采样试验 / 生产用阀门
⑩在天然气生产和输送工业的应用
气举气流流量控制 气管路主阀门压力控制 压缩机喘振控制 天然气压力控制 天然气管路主阀门压力控制 应急关断 天然气广东会器控制 压力控制 压缩机喘振控制 流量控制
四、现在国际上有那些知名公司
国外的执行机构出现较早,一直保持较大优势。西门子公司于1905年生产了世界上第一台电动执行机构。从20世纪90年代初期,国外一些生产电动执行机构的厂商,又开发了新一代的产品占领市场。世界上比较知名的公司主要有以下一些:
1. 英国的罗托克(ROTORK)
从20世纪90年代初期,国外一些生产电动执行机构的厂商,就开发了新的产品占领市场。较早的是英国劳托克(ROTORK),于1995年推出了IQ型智能电动执行机构。IQ系列智能电动执行机构是英国劳托克(ROTORK)公司推出的较早一代智能型电动执行机构,它的执行机构基型是ROTORK多转电动执行机构,在此基础上,加上微处理器和外围芯片电路、软件实现智能控制。它采用红外线手操器来设置执行机构参数,所以能实现无需“开盖”调拭技术。它的限位机构通过霍尔传感器产生数字信号来设定,力矩保护通过测试电机电流和磁场来获得。这种通过霍尔传感器产生数字信号来设定,力矩保护通过测定电机电流和磁场来获得。这种通过电子传感器取代常规的计数器传动机构及凸轮开关组件便于局部工况监视及安全保障并简化调试工作。
2. 美国的乔登(JORDAN)
美国乔登控制公司成立于1955年,从开始到现在一直专业生产电厂挡板电动执行机构,特别是在苛刻工况下(比如:环境温度高,安装位置受限制和不易维护,动作频繁等),乔登的产品一直是世界上大多数用户的首选,这是由于制造商近五十年的经验累积和先进的设计制造思想使然。在这个领域,特别是高调节频度(每小时执行机构能动作的次数达到2000次到4000次)的调节型应用方面,在欧美市场占有率达到70%以上,唯一能和它竞争的是德国HARTMANN& BRAUN,但后者的价格是它的三倍以上。
乔登的主要优势在于高调节频度(2000-4000次/小时),一体化(电机、伺服放大器和传动机构),永久润滑免维护,任意位置角度安装,正齿轮和苏格兰轭传动机构等。目前国内的知名品牌(如:ROTORK,SIPOS,AUMA等)无一例外都采用分体设计,特别是减速箱的寿命是很短的。采用涡轮涡杆传动机构,磨损大,发热量高,传动效率低,寿命短,调节频度最高只能达到1200次/小时。而且要定期润滑维护和不能任意位置安装。
主要系列:SM、LA、MV、VA、EH、TA-1200、MC-1100、SM/LA-3300
3. 德国的EMG
1883 德国AEG集团成立,1900年前后开始生产电动执行器。1946 AEG集团当时欧洲排名第二的电子设备集团(其电厂建设部欧洲排名第一)成立全资子公司EMG,负责电动执行机构业务.1976 EMG 开发出专利的偏心行星齿轮传动机构 并成功应用在其执行器上。1984 AEG集团电厂建设部出售给西门子公司,成为现在西门子的电力集团KWU。 EMG开始设立独立的全球销售网络。1992 在全球有十几万员工的AEG集团被戴姆勒-奔驰集团并购,成为戴姆勒工业部并被分拆。1996 EMG工业集团独立。2003年EMG集团公司在中国设广东会国办事处,开始开拓中国市场。
主要系列:德瑞摩DREHMO(Standard、Matic I、Matic C)
4. ABB
于1988年由分别成立于1883年和1891年的瑞典阿西亚公司和瑞士BBC公司合并成立,总部位于瑞士苏黎世。是电力和自动化技术领域的全球领先公司,ABB集团在全球100多个国家拥有上千家企业,员工139, 000人。
ABB与中国的往来可追溯到本世纪初:早在1907年,ABB就向中国政府提供了一套蒸汽锅炉。随着业务的不断发展,集团于1974年在香港创立了中国地区总部。1994年底把中国地区总部迁至北京。1995年,ABB公司在北京注册了独资的控股公司:阿西亚.布朗. 勃法瑞(中国)投资有限公司,负责中国地区的所有投资活动。目前,ABB中国在上海、广州、重庆、沈阳、武汉、青岛、南京、西安、成都、福州、哈尔滨、天津、大连、济南、杭州、昆明、南宁、深圳、郑州、长春、长沙和香港等地拥有23家销售机构,在北京、上海、广州、重庆、厦门、合肥、新会、中山、香港等地拥有27家合资/独资企业,员工人数达到6000多名。
主要系列:ONTRAC(MOE700、MME 800)
Ontrac系列智能电动执行机构是ABB公司近年推出的智能电动执行机构产品。它的执行机构基型也是多转电动执行机构,它的智能控制器安装在执行机构内,有操作面板直接操作,LCD显示,通过菜单式操作,设置执行机构参数。它采用霍尔传感器来获得位置信号。通过微处理器对电机转差S推算出力矩,并与用户设定的力矩超限值进行比较,一旦超限电机被迫停止运动,微处理器发出报警信号。这种电子式力矩保护方式,省去过程传统的弹簧、机械式开关,调试很方便。该执行机构还能进行变频调速控制及阀门特性修正。除传统控制信号4-20mA可选外,还提供PROFIBUS DP/V1,通讯接口。
5. 德国的哈特曼-布朗(HARTMAN&BRAUN)
主要系列:PME 120
6. 德国的奥马(AUMA)
7.德国的西门子(SIEMENS)
西门子公司是世界自动化行业的“老大”,SIPOS是SIEMENS Positioner的缩写。于一九零五年生产出世界上第一台电动执行机构,至今已有近百年的研究、开发、生产和销售电动执行机构的经验。SIPOS(西博思)为其电动执行机构的注册商标。
SIPOS已被广泛应用于全球各个工业生产领域。中国电厂的所有电动汽机旁路上使用的执行机构几乎全部为原装进口SIPOS。西门子公司还分别于1987年和1992年向中国的两家制造厂出售其SIPOS1系列和SIPOS 3系列的生产技术。西门子公司不断更新技术,相继淘汰了SIPOS 1和SIPOS 3,在全球范围内首次创造性地将先进而又成熟的电机变频控制技术应用于电动执行机构中,采用内置一体化变频器来控制执行机构的电机,并于一九九七年向市场推出面向新世纪的新一代SIPOS 5 系列电动执行机构。
SIPOS 5 于一九九七年底进入中国市场,因其结构简单、技术先进、性能可靠、可进行故障自诊断、智能化程度高且价格适中而备受市场青睐。在短短三年的时间内,中国的七十多家用户相继购买了三千余台,其质量、性能和高性能价格比得到了所有用户的一致赞赏和认同。
为适应市场需要,自一九九九年十月一日起,西门子公司电动执行机构部门从西门子公司庞大的机构中独立出来,以原有注册商标SIPOS为公司名,在德国成为具有独立法人地位的电动执行机构专业性公司:SIPOS AktorikGmbh(西博思电动执行机构有限公司)。西博思公司的总部及生产厂位于德国的纽伦堡市,并已在全球主要国家和地区设有销售和服务机构。
自一九九九年十月一日起,西门子公司所有于电动执行机构有关的业务已全部转至西博思公司,且西门子公司不再生产电动执行机构。独立后的西博思公司仍以SIPOS作为其电动执行机构产品的注册商标,但不再属于西门子公司。西门子公司现在是西博思公司的主要用户之一,西博思公司继续想西门子公司提供产品和服务。
主要系列:SIPOS1、 SIPOS3 、SIPOS 5 Flash
8.法国的伯纳德
法国伯纳德股份有限公司是法中电力协会成员之一,成立于1946年,是世界知名的阀门电动执行器(SERVOMOTEUR)专业生产厂商,其生产的核级阀门电动执行器符合国际标准。自1950年起,法国核电站开始采用该公司的产品。世界上有60多座核电站使用伯纳德的电动执行器。1996年该公司产品开始进入中国市场,为中国的大亚湾、岭澳、秦山、田湾等核电站提供过设备。目前,该公司年产35000多套控制设备,70%销往国外,广泛应用于核电、石油、天然气和水处理等领域。
主要系列:SERVOMOTEUR
9. 意大利的BIFFI
10.美国的柏勒夫(BELLOFRAM)
11.德国PS
12.日本光荣(Unic)
五、JORDAN公司的历史
1955由Chuck Jordan先生创立,1960向电力用户推出风门挡板执行机构,1964推出固态电路控制器,1968推出直行程电动执行机构,1970推出角行程和直行程阀门电动执行机,1978由美国成套供应商配用进入中国市场,1979 ~1990成为并作为Foxboro公司的执行机构分公司,1987首次开发弹簧复位电动执行机构,1990成为独立公司,1991开发并生成采用步进电机的电动执行机构,1992该设计赢得政府设计奖,1995推出智能型数字式伺服控制器,1996通过ISO-9001论证,1997建立公司网站(www.jordancontrols.com),1998推出 HART & Fieldbus 接口,1999推出快速大推力液压电动执行机构,2000推出具有连续调节能力的 SM-6000系列电动执行机构,2001 – 成为独立运作的ROTORK公司。在北京、上海和广东会有服务和备件中心。
六、JORDAN进入中国的情况简述
从1978年山东石横电厂开始进入中国市场,到现在在国内已经有了数十家电力用户,而且从未出过任何问题。从中国的市场来看,目前在电厂的烟风系统(送引风机,磨煤机,排粉机,一次风,二次风等)的挡板,调节阀电动头(给水,凝结水,再循环等)和燃油系统快开阀等方面应用非常广泛。
七、在中国JORDAN主要有哪几种执行机构的业绩
在中国JORDAN主要有角行程(SM);直行程(LA);短直行程(MV、VA)的业绩。
八、在中国执行机构的主要现状
我国的执行机构和伺服放大器是六十年代统一设计的,三十多年来在技术上没有多大广东会,最早的型号有DTZ和DTJ。但近几年(基本是在“九五”期间进行),随着国内对控制要求的不断提高,各相关研究机构和部门也开发出新一代的智能型电动执行机构,性能有很大提高,价格在进口产品的一半以下。
开发机构主要有:上海自动化仪表股份有限公司、四川仪表集团公司、海万迅仪表有限公司、上海锐凯仪表有限公司等。
型号主要有:QSL、QSQ、DKZ-Z、ZKJ-Z、ZILJ、IKJ等。
目前,在中国,执行机构的品牌(含国内品牌和国外品牌)较多,市场竞争较大。国外产品主要集中在中高端市场,而国内产品则集中在低端市场。国外产品质量较优,但价格往往是国产品牌的几倍甚至十倍以上,其在技术和商务方面的投资和努力明显高于国内企业;国内现以有一些产品已能达到较高的性价比,但总体来讲需要加快技术进步和行业激励,加大商务努力。
国产执行机构在各行业应用已比较普遍。但进口执行机构从行业来看,则主要集中在军工、电力、石化、化工、冶金、建材、环保等领域和自动化程度较高的生产线上。从投资来看,进口执行机构应用较多的地方主要是国家投资的大中型企业和支柱产业、外商投资企业、资金充足和融资能广东会的民营企业。
中国经济正在腾飞,做为现今世界第一大制造基地,执行机构的市场潜力仍是非常大的:西部大开发、中部开发、东北老工业基地的振兴等国家重大举措;外资投入的不断加大;老企业的技术更新和改造等都带来了很大的机遇。
现在中国的企业用户已摆脱长期以来的盲目,变得理性化,既不盲目崇洋,也不再一味追求低价。国内企业在紧追和赶超国际先进技术,力争提高知名度;而外国厂商则瞄准中国巨大的市场,在降低价格方面不断的努力,以提高在中国市场的竞争力
以上就是小编对于无锡制氧机外壳模具设计_无锡制氧机外壳模具设计招聘问题和相关问题的解答了,无锡制氧机外壳模具设计_无锡制氧机外壳模具设计招聘的问题希望对你有用!
免责声明: 1、文章部分文字与图片来源网络,如有问题请及时联系我们。 2、因编辑需要,文字和图片之间亦无必然联系,仅供参考。涉及转载的所有文章、图片、音频视频文件 等资料,版权归版权所有人所有。 3、本文章内容如无意中侵犯了媒体或个人的知识产权,请联系我们立即删除,联系方式:请邮件发送至 cnc1698@l63.com