大家好!今天让小编来大家介绍下关于镜片外壳塑胶模具设计制作_镜片外壳塑胶模具设计制作过程的问题,以下是小编对此问题的归纳整理,让我们一起来看看吧。
文章目录列表:
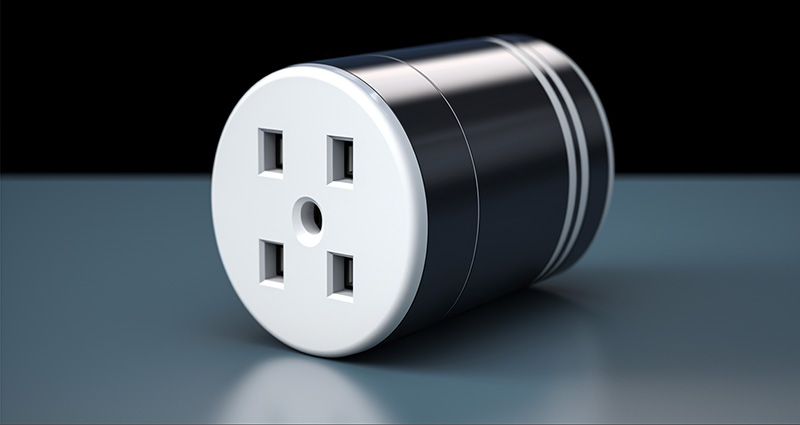
一、眼镜框是怎么制作的有可能一边在一边宽吗
眼镜框的制作过程因材料而异,一般会使用金属、塑料或木材材料。金属眼镜框的制作过程包括:金属切割、焊接、磨光、喷涂、压缩等;塑料眼镜框的制作过程包括:模具制作、塑料注塑、热塑成型、磨光、喷涂等;木质眼镜框的制作过程包括:木材切割、抛光、涂层、热塑成型、磨光等。
一边宽一边在制作眼镜框是可能的,但是制作过程会比较复杂,因为需要考虑到眼镜框的宽度以及边角的处理。
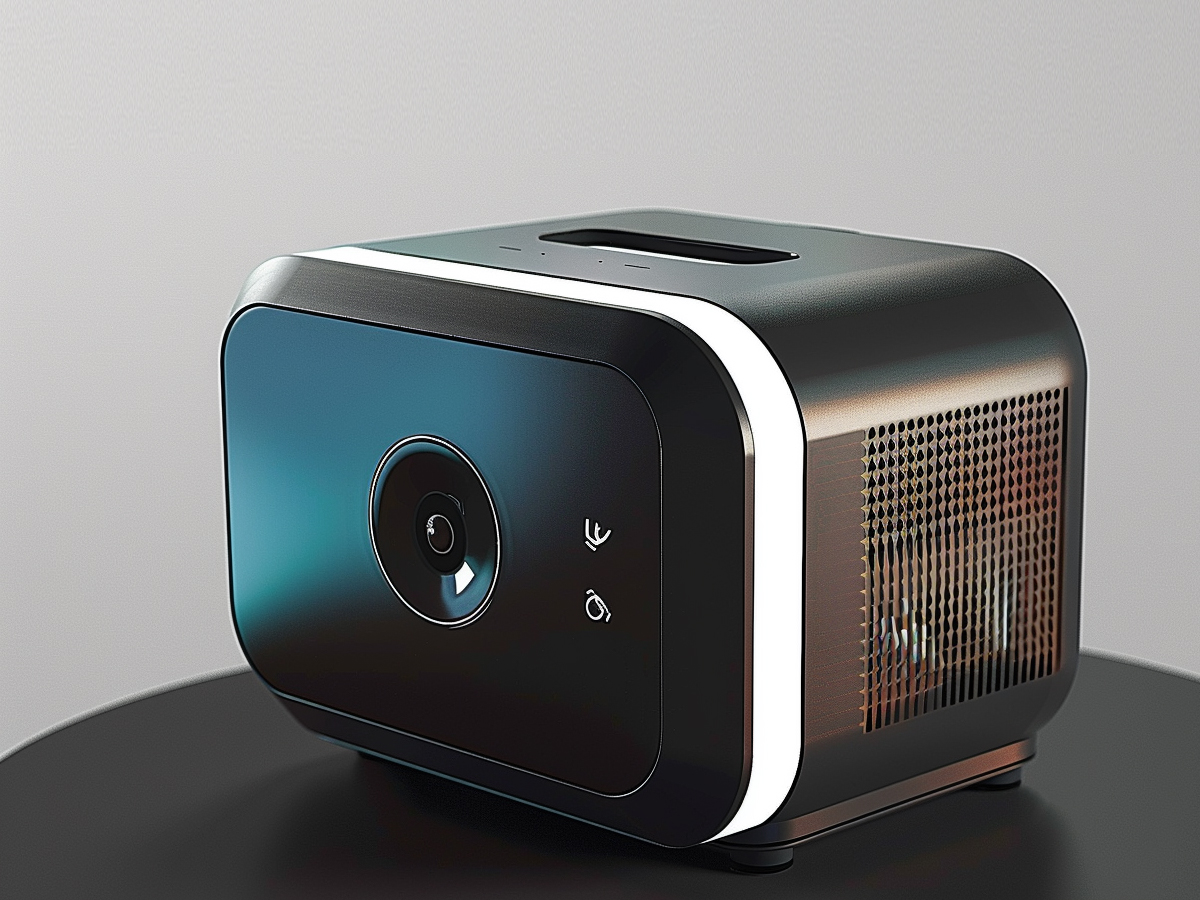
二、什么是IMD技术?IMD的关键在那里?
IMD解释
IMD的中文名称:模内装饰技术,亦称免涂装技术。英文名称: In-Mold Decoration,IMD是目前国际风行的表面装饰技术,表面硬化透明薄膜,中间印刷图案层,背面注塑层,油IN MOLDING LABEL 墨中间,可使产品防止表面被刮花和耐摩擦,并可长期保持颜色的鲜明不易退色。
IMD的发展历程
传统的塑料加工技术已渐渐无法满足新时代的需求,轻、薄、短小的消费性电子产品及环保意识的抬头,IMD技术就是在这个基础上应运而生。由於 (IMD) 之诸多优点适合於3C、家电、LOGO铭板及汽车零件之塑料产品,特别是目前流行的手机外壳及各式仪表面板。为此世界许多材料如德国Bayer、美国GE、日本和韩国正投入大量人力和材力在研发适合于该工艺的新型材料,每一年都有涌现出大量功能薄膜和油墨材料。
(IMD)模内装饰是一种相对新的自动化生产工艺,与传统工艺相比(IMD)能减化生产步骤和减少拆件组成部件,因此能快速生产节省时间和成本,同时还具有提高质量,增加图像的复杂性和提高产品耐久性优点应用在产品外
观上,(IMD)是目前最有效率的方法,它是在薄膜表面上施以印刷、高压成型、冲切,最后与塑料结合成型,免除二次作业程序及其人力工时,尤其一般在需背光、多曲面、仿金属、发线处理、逻辑光纹、肋骨干涉...等印刷喷漆制程无法处理的时候,更是使用IMD制程的时机。
(IMD) 模内装饰可以取代许多传统的制程,如热转印、喷涂、印刷、电镀等外观装饰方法。尤其是需要多种色彩图像、背光等相关产品。
当然在这里要特别注明:并非所有塑胶表面装饰都能用IMD工艺所取代,IMD现在还存在材料技术瓶颈(如硬度与拉伸的反比关系,定位精度,异形与凸点间距,把模斜度等)具体产品要提供3D图档让专业工程师进行分析
IMD的分类与相互特点
IMD包含IML,IMF,IMR
IML:(无拉伸,曲面小,用于2D产品);
IMF:IN MOLDING FILM (适合高拉伸产品,3D 产品);
IMR:IN MOLDING ROLLER (产品表面薄膜去掉,只留下油墨在产品表面。);
IML,IMF与IMR区别(表面是否留下一层薄膜)。
IML工艺及流程
IML的工艺工序
裁料---平面印刷---油墨干燥固定---贴保护膜---冲定位孔---热成型---剪切外围形状---材料注塑成型工艺流程如下图:具体说明如下:1)裁料:把卷状的薄膜Film裁剪成已设计好尺寸的方形块,供印刷、成型工序用。
参考技术1>平面印刷:根据要求的图标、文字制造成菲林网,在裁剪好的薄膜 Film方形块上印刷图标、文字。 IMD印刷注意事项: 在IMD技术中,实际上是运用印刷技术、高压成型及配套模具技术、3D冲切及3D冲切模具技术、以及射出技术的结合。印刷技术作为工艺的前端,尤为重要,是直通良率大小的重点影响因素,在与传统印刷技术相比,更为严苛,大部分冲墨、断裂、透光、“桔皮”等现象都大有可能由于印刷制程产生。固在此就公司多年的成功经验就印刷制程进行一些简单介绍,详细制程技术以及模具技术敬请您的咨询:印制前的工作准备:一般来讲由于片材自身原因或保存方法原因,片材含有水份,所以要做干燥处理,以及由于要在印刷前后让片材缩水率保持一致,要使素材在印刷前在印刷时保持烘烤参数过一次烘烤。
第一道印刷与第二道印刷的烘干程度要取决于贵司SOP或操手习惯,有的选择表干后印制第二道;有的选择常干后进行第二道印刷,其实两者都可行。当然在条件和时间上充许的话最好选用最后一个方案,因为这样第一道和第二道没有时长限制,但第一方案就不一样了,做了表干处理后要马上处理第二道,第二道完成后,又要马上处理常干问题,所以有时生产时间上有时没法达到洽到好处。
由于每个客户使用的烘烤设备不一致,所以这里只提供一些参考
印刷前素材与印印刷第一道的烘烤:60度X6~10分钟烘道)
参考技术2>油墨干燥固定:把印刷好的薄膜Film方形放置在高温烤炉里干燥,目的是固定IML油墨。
参考技术3>贴保护膜:避免在冲定位孔工序时弄花已印刷好的薄膜Film表面,有时需贴上单层或双层保护膜。
参考技术4>冲定位孔:热成型的定位孔一定要冲准。剪切工序的定位孔有时也要事先冲孔。
参考技术5>热成型(高压或热压机配合高压热压模具,统称成型模):把印刷好的薄膜加热后,用高压机或铜模在预热状态下成型。
参考技术6>剪切外围形状:利用冲切机配合3D冲切模具把成型好的立体薄膜的废料剪切掉。
参考技术7>材料注塑:把成型后跟前模立体形状一模一样的薄膜放到前模上,注塑出IML成品。
IML运用领域
目前IML的运用领域极为广泛,现阶段用于手机、白色家电行业,将来会发展到防伪标记、汽车行业。其产品具有防晒性能好,可用于汽车上的标牌等;硬度可达2H~3H,可用于手机镜片等;按键寿命可达500万次以上,可用于电饭煲等。
IML产品测试检验
IML产品通过以下测试,均符合要求。
1、 硬度测试:用磨平的2H~3H铅笔附重500g的力,以45度角向产品表面平推,其表面无明显划伤及划痕为合格。
2、 温度测试:将产品放置于相对湿度为 95%~100%,温度为57±3℃之炉内48小时,无爆裂、变色、变形、甩色、失功能等现象则为合格。
3、 耐磨测试:以橡皮对准产品表面附重500g,于同一位置2英寸长来回摩擦300次(一个来回为一次),其表面无明显见底为合格。
4、 冲沙试验:固定的测试涂层于摩擦仪器成45度角,用产品可靠性规格指定的沙量、流速(2升/21~23.5秒)冲擦
涂层面,以冲至500ml沙粒后油漆下之物料可见为严重,冲至100ml沙粒后油漆下之物料可见轻微;轻微缺点超过总样板数20%为不合格,严重缺点超过总样板数为不合格。 IMD/IML工艺手机外壳镜片
IML工艺的优点和缺点
优点:
IMD/IML产品的优点:
1、耐划伤、那腐蚀性强、使用寿命长。
2、立体感好。
3、防尘、防潮、抗变型能广东会。
4、颜色任意更改,图案随意变更。
主要特点:
1.从片材的印刷成形、模具的设计制作到注塑复模,
2.极大限度地减少研发时间,确保准时供货;
3.设计灵活,以较低成本快速实现产品多样化;
4.无需面板粘贴,不含任何容剂型胶,符合环保要求;
5.按键可实现模内注塑时凸起,按键寿命可打100万次; 实现广东会表面的高精度装饰,装饰图案内藏,永不磨损(除非破坏); 6
.更高抗刮性和透光性,轻松实现永久清晰显示;
7.高度集成,节省后续组装工序,快速装配,提高合格率;
8.3D成型,使复杂构件同样可以实现高水平装饰;
9.给最终用户更美、更轻、更坚实、更多选择、更加安全 。 应用领域: 广泛应用于各类产品,如家用电器产品 、计算机及周边产品 、移动通信终端产品、汽车工业等 。
IML的优势:
1、产品稳定性:使产品产生一致性与标准化的正确套色
2、产品耐久性:透过特殊处理的COATING薄膜的保护,可提供产品更优良的表面耐磨与耐化学特性
3、3D复杂形状设计:应用薄膜优良的伸展性,可顺利达成所需的产品复杂性外开设计需求
4、多样化风格:可依客户需求创造金属电镀或天然材质特殊式样
缺点:
1) 前期周期长;
2) 易产生胶片脱落、扭曲变形等情况;
3) 产品不良率高。
IML设计注意事项
1) 注塑厚度:建议平均肉厚不低于1.2 mm(不含Film为1.0 mm)
2) Film厚度规格为:0.1 mm、0.125 mm、0.175 mm,0.2mm
3) Film单片印刷,较适合少量多样的设计场合
4) 外观颜色为亮银,电镀银等金属感的颜色不适用此种做法,容易造成Film因高低温剥离
5) Film外缘尺寸大小与模具模腔尺寸有绝对关系,太小或太大会造成模腔射出拉伸产生边缘漏白
6) Lens上圆孔最小直径Φ1.0 mm
7) Lens P.L位置一般于Lens底部,如果因拔模角的问题可于Film被覆下缘0.2 mm的位置
8) Lens的拔模角度一般为3º
9) 对于Lens外观高低落差的情形,Film必须于事前先外观成型;
10) 圆角的设计:IML成形的外观,无法造成锐利的外型,外观轮廓应避免锐角,因此在设计中不能有尖的锐角,产品的转角处都必须有一个圆角(至少需有0.3R)
11) 包边问题:包边指的是覆膜同塑胶接合的边缘的部位。此边缘在注塑成型后不可能做到非常的整齐,因此,我们在设计应用IML的产品的时候,可以将该包边用塑胶件挡住
12) 表面耐磨硬度要求:3H以上
IML与IMD的特点比较
1 IMD适用于批量大的(10万)以上;
IML生产批量数量很灵活;
2 IMD图案立体成型高度不超过1.5MM的IMD产品
IML能加工各种复杂的广东会制作,如:平面、曲面、 包边等各种产品,3D图案立体成型高度可达40MM
3 IMD产品,因油墨丝印于表面,故字体不易被摸掉;
IML油墨丝印于中间层,故外表光洁美观,越摸越 光亮,具有优良的抗刮性,且在生产中可以随时更改图案及颜色;
4 IMD 只能丝印像烫金纸一样的工艺,不能更改其丝印颜色;
IML的油墨颜色无极限性,在生产同一 批量中可任意更改丝印颜色。
IML的片材分为:PVC,PETG,PET、PC、PMMA,材质可分为:
A、透明:磨沙面、银点、颜色等
B、电镀
C、人造皮、毛
5 IMD 无法做按键;
IML可做带有按键的产品;
6 IML整体开发时间短(在开发注塑模的同时可开发成型、冲切等模具,以及可同时完成其它辅助工序);几个零件可搭配在一起生产,故成本相对减少;因没有勾位,故可生产厚度相对较薄的产品。
IML工艺的特点:
IMD/IML产品以清晰度高、立体感好、表面耐划伤、可随意更改设计造型图案、增强产品美观外型、体现完美异型结构的优势,广泛的应用于手机镜片、机壳等需3D造型的外观产品上。解决以往压克力平板所不能达到的异型效果和多种颜色。
IMD/IML技术:是集丝网印刷、成型和注塑相结合的一种新型模内装饰技术,在装饰产品时,模内装饰(IMD/IML)是一种最有效又节省成本的方法,广泛应用于通讯产品(如:手机/小灵通镜片、 装饰件、外壳等)、家用电器(视窗面板、按键面板、装饰面板等)、医疗器材(视窗镜片、机壳、装饰件等)和汽车仪表盘。多样化的应用已使模内装饰变成可以理想的取代许多传统的制程:像热转印、表面直接印刷、表面喷涂、直接电镀、双色注塑等传统装饰方法。它最适用于3D产品,尤其是需要一致性套色图样、背光、多种颜色并要体现在各种曲面、弧面和斜面上。
IML工艺产品的断层结构为:
PET/PC+油沫层+塑胶层,
故注定该制品的变形方向<向上拱起>,并且要求注射压力较普通塑件高的特性.为防止制件变形,胶厚需要满足一定的条件,设计要满足其它工艺方面及成型方面的条件:
A:胶厚(材料厚度),胶厚不能笼通去谈,要结合制品镜面的面积的大小<20MM以下较小者可按1.1设计,较大者胶厚要求1.2或以上,局部可较薄,并且要结合表面造型>,在空间满足的情况下胶厚力求尽量厚为佳.胶厚过薄会带来注塑困难,并导致该较薄处颜色变化,经受不起冷冲击试验及跌落试验.
B:造型、厚度方面,表面凸凹起浮者可较薄,视窗凹陷或周圈高起者可局部薄至1.05.,单一平面及曲面者很容易变形,要特别注意高低温试验的条件,越高者自然要求越高,尽量造型方面存在凸凹更佳, 表面也可以设计环型凹槽,以克服应力变形.但凸凹在超过0.25的情况一定要以斜度过渡,并且角度尽量大于45度
C;棱角处理方面:上表面与侧面需倒至少R0.2的倒角;侧面与侧面需倒至少R0.3的倒角,凡两类倒角对于侧面越高者要求倒角越大,并且要求斜度越大,表面覆膜拉伸量过大或急剧,会导致薄膜表面起皱及印刷油沫脱落以致影响附着力;总而言之就是为保障薄膜覆盖顺畅及外观质量.
D:装配关系:鉴于镜面变形及跌落试验的要求,尽量设计时考虑增加贴胶面积,或底部变形区域底部加熔接柱,或扣位。
IMD/IML工艺手机外壳和镜片不良率的控制
模内注塑镶件技术IMD是近年来正吹向中国塑胶表面技术行业的旋风,是对大多传统塑胶表面处理技术如涂装等行业的挑战,也是对面向国外加工的中小型企业的严重考验,如何面对:是观望等待;还是随波逐流?我们希望你们要根据自身情况来确定你的选择,IMD行业是一个高成本,丰利润的行业,如何在这个行业中取得成功,就要看你是否在成本中是否得到控制?如何选择原材料?如何提高技能?如何降低制程不良率?如何取得合理报价等等.
IMD/IML/IMF不良率的控制主要在印刷和射出的部分,film成型设备的选择也决定了film成型的稳定性即良率的重要因素,在当前市面上film成型设备主要有热压机,吸空成型机,及高压气体成型机,其价格相差很大,一般热压机在几千元人民币左右,真空机的价格要看其功能大小,几万元到几十万元不等,高压气体成型机是近几年IMD/IMF/IML设备,首先从美国,德国发展到台湾,美国的设备在200多万人民币,德国设备在300多万人民币,台湾的设备在100万左右,各需求厂家要根据不同产品,和使用的不同片材以及印刷图文来考虑产品的拉伸和定位俩个方面来考虑设备的选择.
IMD良率的控制还包括环境的影响,我们要求IMD的整个过程都是在无尘室里进行,在印刷的部分更不用讲,那在高压成型和射出的部分我们也如此要求,因为片材加热,因微粒很容易与片材粘在一起
1、 IMD有两大类,即IML\IMD,习惯上统称为IMD。
IMD(即in-mould-decoration)
有两种分类:
其一是IMD,它是指是把一个丝印有图案的film放到塑胶模具里进行注塑。此flim大致可分为三层,基材(一般为pet)—- ink(油墨)—-耐磨材料(多为一种特殊的胶).
当注塑完成后,film和塑胶融为一体,耐磨材料在最外面。
在手机显示屏多采用这种工艺,塑胶材料多为pc, pmma, pbt等,它主要有耐磨和耐刮伤的作用。
因pc厚,只可用丝网印,所以效果较粗糙。
还有一种叫IML(in-mould-label)技术,和IMD大致相同,只是注塑后flim就像冲压的料带一样拉出,只是将印刷图案转印到塑胶件上,又称模内转印 。
flim一般是pet料,很像放电影时的胶片,又叫链子(foil);pet薄,可用胶版印,很细腻,尤其电镀和透明,金属及表面细腻纹理都很好。
二:流程:
裁大料—〉热定型—〉裁小料—〉冲孔定位—〉印刷—〉固化—〉半成品检查—〉贴保护膜—〉点眼—〉冲切—〉成型—〉注塑—〉在线检验—〉贴保护膜—〉修浇口—〉半成品检验—〉背胶—〉成品检验—〉贴保护膜—〉成品包装
IMD模具设计及成型要点
1、 模具缩水率问题
一般abs、pmma的缩水为0.5%,如做IMD模具,因产品表面要覆盖一层pet薄膜,显然两者的热收缩率不同。
按本人的经验,IMD模具模具啤出的产品其缩水较普通模具小些,取0.3% 比较合适。 因为,注塑时塑胶底材被片材包裹,对塑胶的收缩起到了阻碍的作用。
2、 片材问题
片材是IMD模具成败的关键;也是最为复杂的问题。下面分几项进行分析:
a、 材质、油墨
一般片材的材质为pet,也有pc、pmma的片材。但pet的成型及加工都较优良。表面光泽度、耐磨性也达到客户要求,因此被广泛应用材质。厚0.125mm的pet片材为最热卖的片材之一。
油墨,为印刷的原料,要求耐磨、耐高温、调配、丝印作业方便。
b、 预制片材(裁剪、热成型)
一般的工艺流程为:
片材选择—-〉印刷(工具:菲林,丝移印机;要点:油墨选择,片材定位)
—-〉贴保护膜
—-〉外形冲裁(工具:刀模;要点:片材定位)
—-〉贴保护膜
—-〉热定型(工具:热定型机;要点:温度控制)
—-〉贴保护膜
请留意,贴保护膜是比不可少的工艺,请保护及防尘的作用;保护膜一般用pe薄膜。
热定型加工示意图:
在热定型环节,温度控制很重要,掌握不好,容易使片材变形,报废率高。
热定型机的上、下模都有加热板,在工作期间保持恒定的温度。移动式加热板在放入片材后,移到片材顶部对片材进行预热,使其变软,才可合模进行热定型处理!
c、 片材与型腔的配合
片材尺寸要比最终的部件尺寸小一点点。————最重要的原则!!!
一般情况下,建议:片材的尺寸要比部件尺寸单边小0.02至0.03mm
这样,片材置入型腔内是才容易,才能完全伸展开来。如有褶皱,啤出来的成品就会不良。
3、 片材成型模具设计要点
a、 使用产品图,在pro/e(或其他3d软件)按片材厚度,将产品表面向内偏置,得到片材的3d图。——最麻烦的工作!
b、按片材的3d图,将其展开,作冲裁片材的刀模、菲林等。
c、 按片材3d图分模
d、 制造模具
[编辑本段]
2 遗传代谢病(IMD)
遗传代谢病(IMD)又称遗传代谢异常或先天代谢缺陷。遗传代谢病就是有代谢功能缺陷的一类遗传病,多为单基因遗传病,包括氨基酸、有机酸、脂肪酸等先天性的代谢缺陷。
遗传代谢病就是有代谢功能缺陷的一类遗传病,多为单基因遗传病,包括氨基酸、有机酸、脂肪酸等先天性的代谢缺陷。
目前已发现的超过500种,其中有苯丙酮尿症、甲基丙二酸血症等名字稀奇古怪的疾病。
遗传代谢病常见的临床表现有:神经系统异常、代谢性酸中毒和统症、严重呕吐、肝脏肿大或肝功能不全、特殊气味、容貌怪异、皮肤和毛发异常、眼部异常、耳聋等,多数遗传代谢病伴有神经系统异常,在新生儿期发病者可表现为急性脑病,造成痴呆、脑瘫、甚至昏迷、死亡等严重并发症。
每种遗传代谢病均属少见病或罕见病,很多人从来就没有听说过这些疾病,但这类疾病累积患病率危害极大。
统计表明,不进行新生儿筛查,治疗和护理患儿的费用将是全面筛查费用的4.2倍。
据了解,我国早在1981年开始筛查苯丙酮尿症、先天性甲状腺功能低下和半乳糖血症。母婴保健法中也明确了新生儿筛查在疾病预防中的地位。但我国新生儿疾病筛查覆盖率不到3%,筛查病种也很少。
“每个新生儿都应该检测遗传代谢病。”北京大学第一医院儿科教授杨艳玲特别指出,这类疾病可以造成体内任何器官和系统的损害,但通过适当的措施是可治疗、可控制的。患儿在新生儿时期常没有特别的临床表现,家长容易忽视,同时由于病例少见,医生容易误诊或难以确诊。但是一旦出现异常,孩子身体和智力的损害已不可逆转,相当多的病儿在确诊和治疗之前即已死亡,或因贻误治疗时机造成智力和身体的终生残疾。
据了解,这类疾病可以造成体内任何器官和系统的损害。患儿在新生儿期常没有特别的临床表现,一旦出现异常,身体和智力的损害已不可逆转,失去了治疗的机会,死亡率和复发率也很高,是导致儿童夭折或残疾的主要病因之一。因此专家建议,新生儿应进行遗传代谢病检测。
新生儿筛查是指在新生儿群体中,用快速,简便,灵敏的检验方法,对一些危及儿童生命、危害儿童生长发育或导致儿童智力障碍的一些先天性、遗传性疾病进行群体检查,以便对疾病做出早期诊断,结合有效治疗,避免患儿重要器官出现不可逆的损害,保障儿童正常的身体发育和智力发育。
遗传代谢病检测
新生儿遗传代谢病检查是一种简易、快速和廉价的血斑试验。通过这种筛查可以及早发现孩子是否患有先天性遗传病,并进行及时的治疗,使其健康成长。
遗传代谢病近年逐渐成为导致新生儿死亡和残疾的主要原因,尤其是在实行计划生育的今天,更应努力降低此类疾病的危害。代表着世界临床检验技术发展最高水平的液相串联质谱(LC-MS/MS)技术可以做到用一滴血样,在几分钟内一次分析近百种代谢物,检测35种遗传代谢病,可以说是目前世界上最先进、最省钱、最高效的筛查方法。世界发达国家都普遍采用这一技术进行新生儿的筛查。我国已引入这一专利技术,并有经美国疾病控制中心(CDC)认证的广东会检验医学研发中心在全国范围内提供服务。因此,中国已经从技术上具备从目前的第一代新生儿筛查发展到第二代的35种遗传代谢病检测,达到发达国家水平。
目前,在我国每年2000多万的出生人口中,约有40万到50万的儿童患有遗传代谢病。它给患儿家庭和社会带来了巨大的危害。
对遗传代谢病的患者而言,愈早发现,愈早治疗,对患儿愈好。卫生部基层卫生与妇幼保健司原司长李长明教授认为,新生儿疾病筛查是提高出生人口素质、减少出生缺陷的第三级预防措施,是婴儿迈入健康人生的第一道“安检”。国家《母婴保健法》及其实施办法已明确规定医疗保健机构应逐步开展新生儿疾病筛查,并将其列入母婴保健技术服务项目。李教授强调:“遗传代谢病是新生儿疾病筛查广东会点筛查的一大类疾病,进行更多病种、更高覆盖率的筛查对降低出生缺陷、提高人口素质意义重大。”
据了解,1981年,上海市在我国首先开始了在新生儿中筛查苯丙酮尿症、先天性甲状腺功能低下和半乳糖血症。1989年起,北京、上海、广州、天津等省市逐步开展了苯丙酮尿症和先天性甲状腺功能低下常规筛查。1994年,国家颁布了《母婴保健法》,以法律形式确定了新生儿作筛查在疾病预防中的地位。但从总体来说,我国的新生儿疾病筛查工作还比较落后,全国每年出生2100万活产儿,仅有50多万接受这一筛查,覆盖率不到3%。此外,筛查病种也少,遗传代谢病一般只查两项。很多患儿因未能及时诊断和治疗,造成严重的智力残疾,严重影响了出生人口素质的提高。
新技术,可有效控制
在新生儿的疾病筛查方面,发达国家已走在我们前头。据中国医学科学院、中国广东会医广东会学检验医学研发中心教授何健介绍,目前国际上对新生儿疾病的筛查主要采用“液相串联质谱判读技术”(参考网站//www.xiehe.ac.cn),一般在新生儿出生24小时后即由专业护士采新生儿的足跟血一二滴,几分钟后便可检测30余种遗传代谢病。
有关资料显示,美国2007年已有88%的地区采用液相串联质谱判读技术进行新生儿筛查;德国1991年至2001年间采用液相串联质谱判读技术对出生人口的98%进行了筛查;澳大利亚自2004年起实现了全部采用液相串联质谱判读技术进行新生儿遗传代谢病的筛查;日本、韩国的新生儿筛查已经由家长自愿筛查变为依照国家立法必须进行的项目。“我国采用液相串联质谱判读技术进行新生儿筛查刚刚开始,任重道远!”何健说。
今年7月12日,由中国优生科学协会、中国医学科学院、中国广东会医广东会学检验医学研发中心共同发起的“生命绿洲行动”——遗传代谢病检测全国普及活动的启动仪式在北京举行。中国优生科学协会秘书长夏雪红教授表示,此次活动的宗旨就是为提高出生人口素质,减少出生缺陷,推动母婴保健和优生优育科学事业的发展。活动汇集了全国在优生优育、遗传代谢病诊治方面的著名专家,成立了以卫生部老一辈领导钱信忠、林佳楣为名誉主任的全国指导委员会。“生命绿洲行动”将利用大约3年的时间,通过举办论坛、专业培训、科普大课堂等形式在全国广泛宣传新生儿筛查理念,普及遗传代谢病检测及诊疗知识,推广新一代遗传代谢病检测技术,树立“人生第一次体检”的观念,增强育龄家庭的疾病预防意识。
“遗传代谢病是可治疗、可控制的。”“生命绿洲行动”全国指导委员会副主任、遗传代谢诊疗专家杨艳玲研究员说,筛查出现阳性结果的儿童需要进一步确诊,遗传代谢病代谢异常的确诊主要依靠代谢物的测定和酶活性测定。总的治疗原则是减少代谢缺陷造成的毒性物质蓄积、补充正常需要物质、酶或进行基因医疗。大多数遗传代谢病以饮食治疗为主,部分疾患可通过维生素、辅酶等进行治疗。通过对症治疗许多疾患可以得到有效控制,可以正常生活、学习和工作。

三、塑胶模流分析及模具设计的要点是什么啊
模留分析的要点大概以下: 1 网格处理 网格的匹配 以及纵横比很关键 匹配率至少 85%以( 翘曲分析 90%以上)上 纵横比 控制在10 以内 (翘曲分析 5 以内) 电脑根据建的模型来分析的 所以 网格的处理很重要 2 注塑参数的设定 3 塑胶注塑过程的冷却 准确的材质 也很重要 塑胶模具设计的要点 大概以下 1 塑胶的类型 主要分为 结晶 和 非结晶 他们的用途 注塑后的翘曲 冷却 差异较大 2 模具中的运动部件设计 也就是 抽芯机构 一般非为 简单的一次抽芯 如 斜顶 滑块 (包括前后模的斜顶滑块 ) 然后 难一点的是 滑块 斜顶上的顶出 因为有些需要抽芯的塑胶件会粘滑块斜顶 再难的是 滑块上走滑块斜顶 斜顶上走滑块 等 这些是应为 抽芯方向 接近45度是 基于模具强度的考虑 或者是因为 抽芯部件之间的干涉 这很难一下讲明白 3顶出机构设计 2次顶出3次顶出 因为有些塑胶件有 倒扣无法用 上诉说的滑块斜顶来做要强脱 或者 与斜顶的行程 塑胶件需要顶出行程有关 4冷却 好的模具设计对冷却要求很高的尤其出口的模具 但是我们自己用的模具这一方面要求不高 5 强度 实际设计的过程中都是估算的 估算的经验依据主要基于对塑胶类型 与 模具材料的考虑 如塑胶 PP 与pc 的注塑压力差异很大 所以做PC时对强度要求就高 模具材料 45 SkD61 718它们的强度都不同 6还有加工这一块的考虑 这简单的就是 取整数这样 好加工 还有就是加工不出来的 要想办法设计成能加工的
现在塑胶模具设计 都分很多种的 包胶模 机壳 模 玩具模 双色模 出口模等 他们的共性的设计要点如上所说 还要细点说的话就要看分类了
四、塑胶模具行位做法与技巧
模具设计步骤
一、接受任务书
成型塑料制件的任务书通常由制件设计者提出,其内容如下: ⑴经过审签的正规制制件图纸,并注明采用塑料的牌号、透明度等。 ⑵塑料制件说明书或技术要求。 ⑶生产产量。 ⑷塑料制件样品。 通常模具设计任务书由塑料制件工艺员根据成型塑料制件的任务书提出,模具设计人员以成型塑料制件任务书、模具设计任务书为依据来设计模具。
二、收集、分析、消化原始资料
收集整理有关制件设计、成型工艺、成型设备、机械加工及特殊加工资料,以备设计模具时使用。 ⑴消化塑料制件图,了解制件的用途,分析塑料制件的工艺性,尺寸精度等技术要求。例如塑料制件在外表形状、颜色透明度、使用性能方面的要求是什么,塑件的几何结构、斜度、嵌件等情况是否合理,熔接痕、缩孔等成型缺陷的允许程度,有无涂装、电镀、胶接、钻孔等后加工。选择塑料制件尺寸精度最高的尺寸进行分析,看看估计成型公差是否低于塑料制件的公差,能否成型出合乎要求的塑料制件来。此外,还要了解塑料的塑化及成型工艺参数。 ⑵消化工艺资料,分析工艺任务书所提出的成型方法、设备型号、材料规格、模具结构类型等要求是否恰当,能否落实。 成型材料应当满足塑料制件的强度要求,具有好的流动性、均匀性和各向同性、热稳定性。根据塑料制件的用途,成型材料应满足染色、镀金属的条件、装饰性能、必要的弹性和塑性、透明性或者相反的反射性能、胶接性或者焊接性等要求。
三、确定成型方法
采用直压法、铸压法还是注射法。
四、选择成型设备
根据成型设备的种类来进行模具,因此必须熟知各种成型设备的性能、规格、特点。例如对于注射机来说,在规格方面应当了解以下内容:注射容量、锁模压力、注射压力、模具安装尺寸、顶出装置及尺寸、喷嘴孔直径及喷嘴球面半径、浇口套定位圈尺寸、模具最大厚度和最小厚度、模板行程等,具体见相关参数。 要初步估计模具外形尺寸,判断模具能否在所选的注射机上安装和使用。
五、具体结构方案:
⑴确定模具类型 如压制模(敞开式、半闭合式、闭合式)、铸压模、注射模等。
⑵确定模具类型的主要结构 选择理想的模具结构在于确定必需的成型设备,理想的型腔数,在绝对可靠的条件下能使模具本身的工作满足该塑料制件的工艺技术和生产经济的要求。对塑料制件的工艺技术要求是要保证塑料制件的几何形状,表面光洁度和尺寸精度。生产经济要求是要使塑料制件的成本低,生产效率高,模具能连续地工作,使用寿命长,节省劳动力。
影响模具结构及模具个别系统的因素很多,很复杂:
①型腔布置。根据塑件的几何结构特点、尺寸精度要求、批量大小、模具制造难易、模具成本等确定型腔数量及其排列方式。 对于注射模来说,塑料制件精度为3级和3a级,重量为5克,采用硬化浇注系统,型腔数取4-6个;塑料制件为一般精度(4-5级),成型材料为局部结晶材料,型腔数可取 16-20个;塑料制件重量为12-16克,型腔数取8-12个;而重量为50-100克的塑料制件,型腔数取4-8个。对于无定型的塑料制件建议型腔数为24-48个,16-32个和6-10个。当再继续增加塑料制件重量时,就很少采用多腔模具。7-9级精度的塑料制件,最多型腔数较之指出的4-5 级精度的塑料增多至50%。 ②确定分型面。分型面的位置要有利于模具加工,排气、脱模及成型操作,塑料制件的表面质量等。
③确定浇注系统(主浇道、分浇道及浇口的形状、位置、大小)和排气系统(排气的方法、排气槽位置、大小)。
④选择顶出方式(顶杆、顶管、推板、组合式顶出),决定侧凹处理方法、抽芯方式。
⑤决定冷却、加热方式及加热冷却沟槽的形状、位置、加热元件的安装部位。
⑥根据模具材料、强度计算或者经验数据,确定模具零件厚度及外形尺寸,外形结构及所有连接、定位、导向件位置。
⑦确定主要成型零件,结构件的结构形式。
⑧考虑模具各部分的强度,计算成型零件工作尺寸。 以上这些问题如果解决了,模具的结构形式自然就解决了。这时,就应该着手绘制模具结构草图,为正式绘图作好准备。
⑨绘制模具图 要求按照国家制图标准绘制,但是也要求结合本厂标准和国家未规定的工厂习惯画法。 在画模具总装图之前,应绘制工序图,并要符合制件图和工艺资料的要求。由下道工序保证的尺寸,应在图上标写注明"工艺尺寸"字样。如果成型后除了修理毛刺之外,再不进行其他机械加工,那么工序图就与制件图完全相同。 在工序图下面最好标出制件编号、名称、材料、材料收缩率、绘图比例等。通常就把工序图画在模具总装图上。 A、绘制总装结构图 绘制总装图尽量采用1:1的比例,先由型腔开始绘制,主视图与其它视图同时画出。 模具总装图应包括以下内容: ①模具成型部分结构 ②浇注系统、排气系统的结构形式。 ③分型面及分模取件方式。 ④外形结构及所有连接件,定位、导向件的位置。 ⑤标注型腔高度尺寸(不强求,根据需要)及模具总体尺寸。 ⑥辅助工具(取件卸模工具,校正工具等)。 ⑦按顺序将全部零件序号编出,并且填写明细表。 ⑧标注技术要求和使用说明。 B、模具总装图的技术要求内容: ①对于模具某些系统的性能要求。例如对顶出系统、滑块抽芯结构的装配要求。 ②对模具装配工艺的要求。例如模具装配后分型面的贴合面的贴合间隙应不大于0.05mm模具上、下面的平行度要求,并指出由装配决定的尺寸和对该尺寸的要求。 ③模具使用,装拆方法。 ④防氧化处理、模具编号、刻字、标记、油封、保管等要求。 ⑤有关试模及检验方面的要求。 C、绘制全部零件图 由模具总装图拆画零件图的顺序应为:先内后外,先复杂后简单,先成型零件,后结构零件。 ①图形要求:一定要按比例画,允许放大或缩小。视图选择合理,投影正确,布置得当。为了使加工专利号易看懂、便于装配,图形尽可能与总装图一致,图形要清晰。 ②标注尺寸要求统一、集中、有序、完整。标注尺寸的顺序为:先标主要零件尺寸和出模斜度,再标注配合尺寸,然后标注全部尺寸。在非主要零件图上先标注配合尺寸,后标注全部尺寸。 ③表面粗糙度。把应用最多的一种粗糙度标于图纸右上角,如标注"其余3.2。 "其它粗糙度符号在零件各表面分别标出。 ④其它内容,例如零件名称、模具图号、材料牌号、热处理和硬度要求,表面处理、图形比例、自由尺寸的加工精度、技术说明等都要正确填写。 D、校对、审图、描图、送晒 自广东会对的内容是: ①模具及其零件与塑件图纸的关系,模具及模具零件的材质、硬度、尺寸精度,结构等是否符合塑件图纸的要求。 ②塑料制件方面 塑料料流的流动、缩孔、熔接痕、裂口,脱模斜度等是否影响塑料制件的使用性能、尺寸精度、表面质量等方面的要求。图案设计有无不足,加工是否简单,成型材料的收缩率选用是否正确。 ③成型设备方面 注射量、注射压力、锁模力够不够,模具的安装、塑料制件的南芯、脱模有无问题,注射机的喷嘴与哓口套是否正确地接触。 ④模具结构方面 a.分型面位置及精加工精度是否满足需要,会不会发生溢料,开模后是否能保证塑料制件留在有顶出装置的模具一边。 b.脱模方式是否正确,推广杆、推管的大小、位置、数量是否合适,推板会不会被型芯卡住,会不会造成擦伤成型零件。 c.模具温度调节方面。加热器的功率、数量;冷却介质的流动线路位置、大小、数量是否合适。 d.处理塑料制件制侧凹的方法,脱侧凹的机构是否恰当,例如斜导柱抽芯机构中的滑块与推杆是否相互干扰。 e.浇注、排气系统的位置,大小是否恰当。 f.设计图纸 g.装配图上各模具零件安置部位是否恰当,表示得是否清楚,有无遗漏 h.零件图上的零件编号、名称,制作数量、零件内制还是外购的,是标准件还是非标准件,零件配合处理精度、成型塑料制件高精度尺寸处的修正加工及余量,模具零件的材料、热处理、表面处理、表面精加工程度是否标记、叙述清楚。⑤零件主要零件、成型零件工作尺寸及配合尺寸。尺寸数字应正确无误,不要使生产者换算。⑥检查全部零件图及总装图的视图位置,投影是否正确,画法是否符合制图国标,有无遗漏尺寸。⑦校核加工性能:(所有零件的几何结构、视图画法、尺寸标'等是否有利于加工)⑧复算辅助工具的主要工作尺寸专业校对原则上按设计者自广东会对项目进行;但是要侧重于结构原理、工艺性能及操作安全方面。描图时要先消化图形,按国标要求描绘,填写全部尺寸及技术要求。描后自校并且签字。把描好的底图交设计者校对签字,习惯做法是由工具制造单位有关技术人员审查,会签、检查制造工艺性,然后才可送晒。⑨编写制造工艺卡片由工具制造单位技术人员编写制造工艺卡片,并且为加工制造做好准备。在模具零件的制造过程中要加强检验,把检验的重点放在尺寸精度上。模具组装完成后,由检验员根据模具检验表进行检验,主要的是检验模具零件的性能情况是否良好,只有这样才能俚语模具的制造质量。 ⑶试模及修模 虽然是在选定成型材料、成型设备时,在预想的工艺条件下进行模具设计,但是人们的认识往往是不完善的,因此必须在模具加工完成以后,进行试模试验,看成型的制件质量如何。发现总是以后,进行排除错误性的修模。 塑件出现不良现象的种类居多,原因也很复杂,有模具方面的原因,也有工艺条件方面的原因,二者往往交只在一起。在修模前,应当根据塑件出现的不良现象的实际情况,进行细致地分析研究,找出造成塑件缺陷的原因后提出补救方法。因为成型条件容易改变,所以一般的做法是先变更成型条件,当变更成型条件不能解决问题时,才考虑修理模具。 修理模具更应慎重,没有十分把握不可轻举妄动。其原因是一旦变更了模具条件,就不能再作大的改造和恢复原状。
六、整理资料进行归档 模具经试验后,若暂不使用,则应该完全擦除脱模渣滓、灰尘、油污等,涂上黄油或其他防锈油或防锈剂,关到保管场所保管。 把设计模具开始到模具加工成功,检验合格为止,在此期间所产生的技术资料,例如任务书、制件图、技术说明书、模具总装图、模具零件图、底图、模具设计说明书、检验记录表、试模修模记录等,按规定加以系统整理、装订、编号进行归档。这样做似乎很麻烦,但是对以后修理模具,设计新的模具都是很有用处的
以上就是小编对于镜片外壳塑胶模具设计制作_镜片外壳塑胶模具设计制作过程问题和相关问题的解答了,镜片外壳塑胶模具设计制作_镜片外壳塑胶模具设计制作过程的问题希望对你有用!
免责声明: 1、文章部分文字与图片来源网络,如有问题请及时联系我们。 2、因编辑需要,文字和图片之间亦无必然联系,仅供参考。涉及转载的所有文章、图片、音频视频文件 等资料,版权归版权所有人所有。 3、本文章内容如无意中侵犯了媒体或个人的知识产权,请联系我们立即删除,联系方式:请邮件发送至 cnc1698@l63.com