大家好!今天让小编来大家介绍下关于塑料制品外壳结构设计图_塑料制品外壳结构设计图片的问题,以下是小编对此问题的归纳整理,让我们一起来看看吧。
文章目录列表:
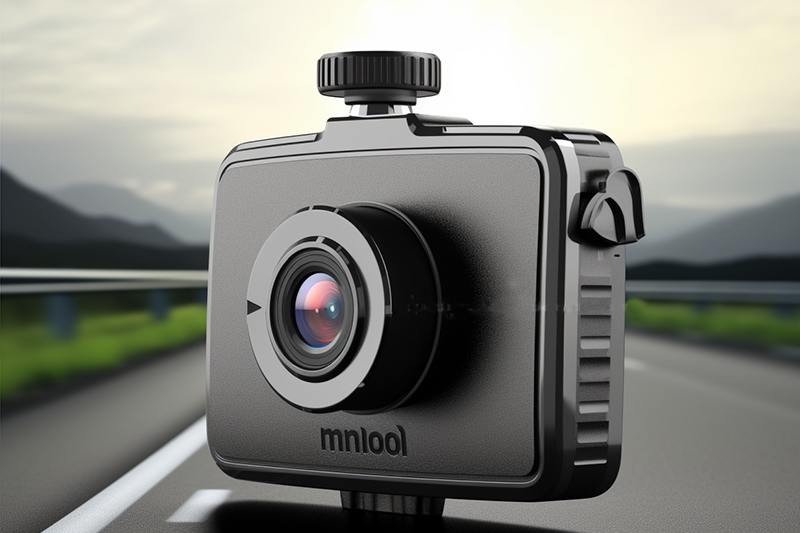
一、产品的塑料外壳是怎样做的
塑料外壳有吸塑成型和注塑成型二种,都是开好模模后,用机床成型。
使用较多的就是ABS,PC+ABS,PC几种材料。

二、塑料外观件和结构件区别
登录
首页
学习
实践
活动
工具
TVP
枫桦
57 篇文章
关注
五金
产品结构设计和塑胶产品设计的异同
2022-08-02 13:47:14阅读 1430
1、外形方面。
很多朋友往往印象流,认为五金件多简单,其实那是因为你没见过。有条件可以去看看轿车的四门两盖,尤其是侧围,你就知道冲压件也有复杂的了。不过那些一般是用UG或者CATIA设计了,还会需要Autoform去模拟成型过程,Thinkdesign去处理回弹问题等。而塑胶件多形状复杂,建模、抽壳都费神。
2、结构方面。
五金件多为大型,尺寸相对不精密,联接方式一般为铆接,焊接,锁螺丝,也有互扣的情况,塑胶件在其上多为装饰件,如不锈钢抽油烟机,还要考虑散热,电磁辐射,噪音,变形整形,防鼠及接地问题;
塑胶件多为小型,尺寸要示精密,联接方式一般为扣位,超声,锁螺丝,五金件在其上多为装饰件,如手机,有时还会考虑防水,防尘,防静电,防电磁辐射,有喇叭的话还有前后音腔的问题,嚣叫的问题。
3、表面处理方面。
五金件一般为表面拉丝,抛光,喷砂,阳极氧化,电镀,电泳,丝印,喷油,镭雕,五金件还有防锈,防静电和防导电的问题;
塑胶件一般为喷油,丝印,烫金,电镀(水镀,真空镀),水转印,IMD,电镀后拉丝,UV,PU,电铸,镭雕,双色
4、成型方式
五金件一般为冲压,拉伸,折弯,翻边,压铸,精铸,型材
塑胶件一般为注塑,吹塑
5、跟模及缺陷防止
五金件一般来说跟模较简单,产品缺陷主要集中于压铸这一块
塑胶件跟模就麻烦多了,还要和注塑,标准件供应商(包括五金的,电子的,胶水的,包材的)打交道
总的说来,你在五金件方面有三年设计经验,应聘如下企业是没问题的,如做机柜的,做安防的,但要涉及到数码类产品的话,五金件只占其中一部分,主要为装饰用,所以建议你先做做安防的东东,逐步接触塑胶类产品,相信两三年后就能集五金塑胶于一身,成为全能大师。
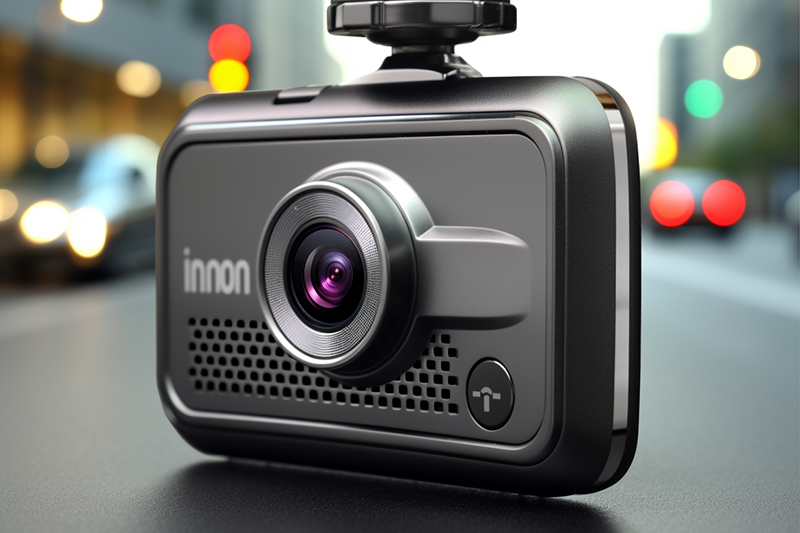
三、家用电器的外壳制品,有很多种加工技术吗?都有哪些?
近年来,一些塑料加工新技术、新设备在家用电器塑料制品成型中得到大量应用,如精密注塑、快速成型技术、熔芯注塑技术、气辅/水辅注塑成型技术等。传统的家用电器用塑料制品的成型加工方法主要有注塑成型、挤出成型、热成型、中空成型、层压成型、压缩模塑、传递模塑、泡沫塑料成型、浇注成型、嵌铸、封铸等,其中以注塑成型为主。
1、精密注塑可以保证制品在尺寸和重量方面具有高精度和高重复性。采用这一技术的注塑机可以实现高压、高速注射。由于其控制方式通常为开环或闭环控制,因此可以对注塑工艺参数实现高精度控制。通常,精密注塑对模具的精度要求较高。目前,国内已能生产中小型精密注塑机。
2、快速成型技术是伴随着家用电器品种向多样化方向发展以及不断的更新换代而快速发展起来的,主要用于制备家用电器用塑料外壳。这一技术的优点是,不需要模具即可实现塑件的小批量生产。目前,比较成熟的快速成型方法有激光扫描成型和液体光固化成型,其中激光扫描成型法应用较多。激光扫描设备是由激光光源、扫描装置、撒粉装置和计算机组成。其加工过程是,由计算机控制的激光头按一定轨迹进行扫描,在激光经过的位置上,塑料微粉受热熔化并粘结在一起,每扫描完一次,微粉装置就撒一层薄粉,这样,经过反复扫描,就形成了具有一定形状和尺寸的制品。现在,国内已有一些企业能够生产激光扫描成型机和塑料微粉,但设备性能不稳定,微粉的品种牌号也少。
3、熔芯注塑技术通常被用于成型对空腔粗糙度和精度要求较高的、不能用中空成型或旋转成型方法加工的异型空腔制品。目前,该技术在国外的应用已比较成熟,但在国内尚处于个别应用状态。该技术的加工原理是,先成型出构成空腔的芯型,然后再用芯型作为嵌件注塑成型。在注塑件的加热作用下,使芯型熔化流出,从而形成了空腔。使用该技术最重要的一点是需要掌握好芯型材料和塑件的熔点。通常,芯型材料可根据具体情况而选用广东会塑料、热塑型弹性体或低熔点金属如铅、锡等。
4、气辅/水辅注塑成型用途广泛,可成型多种类型的注塑件,其典型制品是电视机外壳。注塑时,可将气体或过热水与塑料熔体几乎同步地注入型腔中。此时,塑料熔体将气体或过热水包覆,成型的塑料制品为夹层结构,塑件定型后排出气体或水即可脱模。此类制品具有省料、收缩小、外观好、刚性好的优点。成型设备的关键部分是气辅或水辅装置及其控制软件。近年来,国内虽然对此研究较多,应用速度也较快,但国产设备尚不稳定。
5、电磁动态注塑成型技术是由华南广东会大学瞿金平先生发明的。该技术通过电磁力的作用使螺杆在轴向产生往复振动。由于在预塑化阶段使塑料得以微观塑化,从而使保压阶段的塑件结构更密实,并减小了制品的内应力。这一技术可用于成型要求较高的制品如光碟。当被用于普通制品的成型时,可提高制品的质量。
6、覆膜注塑成型技术与设备在国外的应用已比较成熟。使用该技术时,需要在注塑前将专用印花装饰塑料膜夹在模具内,然后注塑成型。印花膜受热变形后可贴合在塑件表面,不但美观牢固,而且还省去了后装饰步骤。
一般情况下,家用电器塑料制品对塑料模具及阻燃塑料的需求量非常大,用量最多的为:阻燃PP,阻燃ABS,其次就是阻燃PBT等阻燃材料。
欢迎提问,一起交流学习——家电外壳塑料颗粒的生产厂^_^
四、注塑模具都有哪些结构组成?
模具的结构虽然由于塑料品种和性能、塑料制品的形状和结构以及注射机的类型等不同而可能千变万化,但是基本结构是一致的。模具主要由浇注系统、调温系统、成型零件和结构零件组成。其中浇注系统和成型零件是与塑料直接接触部分,并随塑料和制品而变化,是塑模中最复杂,变化最大,要求加工光洁度和精度最高的部分。
注塑模具由动模和定模两部分组成,动模安装在注射成型机的移动模板上,定模安装在注射成型机的固定模板上。在注射成型时动模与定模闭合构成浇注系统和型腔,开模时动模和定模分离以便取出塑料制品。为了减少繁重的模具设计和制造工作量,注塑模大多采用了标准模架。
一、浇注系统
浇注系统是指塑料从射嘴进入型腔前的流道部分,包括主流道、冷料穴、分流道和浇口等。
浇注系统又称流道系统,它是将塑料熔体由注射机喷嘴引向型腔的一组进料通道,通常由主流道、分流道、浇口和冷料穴组成。它直接关系到塑料制品的成型质量和生产效率。
1、主流道
它是模具中连接注塑机射嘴至分流道或型腔的一段通道。主流道顶部呈凹形以便与喷嘴衔接。主流道进口直径应略大于喷嘴直径(0.8mm)以避免溢料,并防止两者因衔接不准而发生的堵截。进口直径根据制品大小而定,一般为4-8mm。主流道直径应向内扩大呈3°到5°的角度,以便流道赘物的脱模。
2、冷料穴
它是设在主流道末端的一个空穴,用以捕集射嘴端部两次注射之间所产生的冷料,从而防止分流道或浇口的堵塞。如果冷料一旦混入型腔,则所制制品中就容易产生内应力。冷料穴的直径约8-,深度为6mm。为了便于脱模,其底部常由脱模杆承担。脱模杆的顶部宜设计成曲折钩形或设下陷沟槽,以便脱模时能顺利拉出主流道赘物。
3、分流道
它是多槽模中连接主流道和各个型腔的通道。为使熔料以等速度充满各型腔,分流道在塑模上的排列应成对称和等距离分布。分流道截面的形状和尺寸对塑料熔体的流动、制品脱模和模具制造的难易都有影响。如果按相等料量的流动来说,则以圆形截面的流道阻力最小。但因圆柱形流道的比表面小,对分流道赘物的冷却不利,而且这种分流道必须开设在两半模上,既费工又不易对准。因此,经常采用的是梯形或半圆形截面的分流道,且开设在带有脱模杆的一半模具上。流道表面必须抛光以减少流动阻力提供较快的充模速度。流道的尺寸决定于塑料品种,制品的尺寸和厚度。对大多数热塑性塑料来说,分流道截面宽度均不超过8mm,特大的可达10-,特小的2-3mm。在满足需要的前提下应尽量减小截面积,以增加分流道赘物和延长冷却时间。
4、浇口
它是接通主流道(或分流道)与型腔的通道。通道的截面积可以与主流道(或分流道)相等,但通常都是缩小的。所以它是整个流道系统中截面积最小的部分。浇口的形状和尺寸对制品质量影响很大。
浇口的作用是:
A、控制料流速度:
B、在注射中可因存于这部分的熔料早凝而防止倒流:
C、使通过的熔料受到较强的剪切而升高温度,从而降低表观粘度以提高流动性:
D、便于制品与流道系统分离。浇口形状、尺寸和位置的设计取决于塑料的性质、制品的大小和结构。一般浇口的截面形状为矩形或圆形,截面积宜小而长度宜短,这不仅基于上述作用,还因为小浇口变大较容易,而大浇口缩小则很困难。浇口位置一般应选在制品最厚而又不影响外观的地方。浇口尺寸的设计应考虑到塑料熔体的性质。型腔它是模具中成型塑料制品的空间。用作构成型腔的组件统称为成型零件。各个成型零件常有专用名称。
构成制品外形的成型零件称为凹模(又称阴模),构成制品内部形状(如孔、槽等)的称为型芯或凸模(又称阳模)。设计成型零件时首先要根据塑料的性能、制品的几何形状、尺寸公差和使用要求来确定型腔的总体结构。其次是根据确定的结构选择分型面、浇口和排气孔的位置以及脱模方式。最后则按控制品尺寸进行各零件的设计及确定各零件之间的组合方式。塑料熔体进入型腔时具有很高的压力,故成型零件要进行合理地选材及强度和刚度的校核。为保证塑料制品表面的光洁美观和容易脱模,凡与塑料接触的表面,其粗糙度Ra>0.,而且要耐腐蚀。成型零件一般都通过热处理来提高硬度,并选用耐腐蚀的钢材制造。
二、调温系统
为了满足注射工艺对模具温度的要求,需要有调温系统对模具的温度进行调节。对于热塑性塑料用注塑模,主要是设计冷却系统使模具冷却。模具冷却的常用办法是在模具内开设冷却水通道,利用循环流动的冷却水带走模具的热量;模具的加热除可利用冷却水通道热水或蒸汽外,还可在模具内部和周围安装电加热元件。
三、成型部件
成型零件是指构成制品形状的各种零件,包括动模、定模和型腔、型芯、成型杆以及排气口等。成型部件由型芯和凹模组成。型芯形成制品的内表面,凹模形成制品的外表面形状。合模后型芯和型腔便构成了模具的型腔。按工艺和制造要求,有时型芯和凹模由若干拼块组合而成,有时做成整体,仅在易损坏、难加工的部位采用镶件。
1、排气口
它是在模具中开设的一种槽形出气口,用以排出原有的及熔料带入的气体。熔料注入型腔时,原存于型腔内的空气以及由熔体带入的气体必须在料流的尽头通过排气口向模外排出,否则将会使制品带有气孔、接不良、充模不满,甚至积存空气因受压缩产生高温而将制品烧伤。一般情况下,排气孔既可设在型腔内熔料流动的尽头,也可设在塑模的分型面上。后者是在凹模一侧开设深0.03-0.2mm,宽1.5-6mm的浅槽。注射中,排气孔不会有很多熔料渗出,因为熔料会在该处冷却固化将通道堵死。排气口的开设位置切勿对着操作人员,以防熔料意外喷出伤人。此外,亦可利用顶出杆与顶出孔的配合间隙,顶块和脱模板与型芯的配合间隙等来排气。
四、结构零件
它是指构成模具结构的各种零件,包括:导向、脱模、抽芯以及分型的各种零件。如前后夹板、前后扣模板、承压板、承压柱、导向柱、脱模板、脱模杆及回程杆等。
1、导向部件
为了确保动模和定模在合模时能准确对中,在模具中必须设置导向部件。在注塑模中通常采用四组导柱与导套来组成导向部件,有时还需在动模和定模上分别设置互相吻合的内、外锥面来辅助定位。
2、推出机构
在开模过程中,需要有推出机构将塑料制品及其在流道内的凝料推出或拉出。推出固定板和推板用以夹持推杆。在推杆中一般还固定有复位杆,复位杆在动、定模合模时使推板复位。
3、侧抽芯机构
有些带有侧凹或侧孔地塑料制品,在被推出以前必须先进行侧向分型,抽出侧向型芯后方能顺利脱模,此时需要在模具广东会置侧抽芯机构。
注射装置是使树脂材料受热融化后射入模具内的装置。从料头把树脂挤入料筒中,通过螺杆的转动将熔体输送至机筒的前端。在那个过程中,在加热器的作用下加热使机筒内的树脂材料受热,在螺杆的剪切应力作用下使树脂成为熔融状态,将相当于成型品及主流道,分流道的熔融树脂滞留于机筒的前端(称之为计量),螺杆的不断向前将材料射入模腔。当熔融树脂在模具内流动时,须控制螺杆的移动速度(射出速度),并在树脂充满模腔后用压力(保压力)进行控制。当螺杆位置,注射压力达到一定值时我们可以将速度控制切换成压力控制。
以上就是小编对于塑料制品外壳结构设计图_塑料制品外壳结构设计图片问题和相关问题的解答了,塑料制品外壳结构设计图_塑料制品外壳结构设计图片的问题希望对你有用!
免责声明: 1、文章部分文字与图片来源网络,如有问题请及时联系我们。 2、因编辑需要,文字和图片之间亦无必然联系,仅供参考。涉及转载的所有文章、图片、音频视频文件 等资料,版权归版权所有人所有。 3、本文章内容如无意中侵犯了媒体或个人的知识产权,请联系我们立即删除,联系方式:请邮件发送至 cnc1698@l63.com